Table of Contents
Basic woodturning strokes for beginners using traditional tools include the spindle roughing gouge for shaping on a flywheel lathe, skew chisel for planing, spindle gouge for detailing, parting tool for cutting dovetails and grooves, bowl gouge for shaping bowls on a pole lathe, and scrapers for finishing and smoothing. Practice these techniques safely to build woodturning skills.
Basic Woodturning Techniques and Strokes
Roughing Gouge
Once you’ve chosen your wood, it’s time to shape it. Roughing is the first step. It involves a roughing gouge, a tool essential for beginners. This technique quickly removes material from the outside of the turning blank.
Roughing sets the stage for all that follows. I always start with firm grips on both handles of my gouge. Then, I use even pressure as I move along the wood’s surface. This helps me create a cylindrical shape without deep gouges or uneven spots.
Smoothing Stroke
After roughing comes smoothing. The goal here is to refine what you’ve shaped so far. You’ll switch tools, often using a more minor gouge or other specialized chisels.
This part is satisfying because it starts revealing the final form of my project. My strokes are lighter during smoothing than when roughing out material—I focus more on control than removal rate.
Finishing Touches
The last phase is finishing your workpiece with fine cuts and sandpaper if needed. Here’s where patience pays off: delicate strokes can make all the difference in appearance and texture.
When I finish my projects, I don’t rush these final touches, ensuring smooth surfaces and crisp details. Remember: practice makes perfect with these techniques!
Step-by-Step Guide on Turning Your First Bowl
Select Wood
Start by choosing a suitable wood. Look for a piece without cracks or large knots. Softwoods can be easier for beginners to turn but may need to hold details better.
I recommend hardwoods like maple or cherry for their durability and fine grain. These woods produce smoother bowls with a professional feel, even for a beginner.
Shape Exterior
Mount the wood block securely on your lathe. Begin shaping the exterior of your bowl with the basic strokes you’ve learned earlier. Keep tools sharp and move slowly.
Use bowl gouges to create smooth curves, remembering to keep the angle rubbing against the wood for control. Taking my time here often sets up success later in finishing touches.
Hollow Inside
Once satisfied with the shape, start hollowing out your bowl’s interior. This step requires steady hands and patience as you remove material bit by bit.
Maintain consistent pressure and listen to the cutting sound—it tells you if you’re going too fast or slow. My first attempts taught me that rushing leads to mistakes; it’s better to progress gradually.
Sand Smoothly
After shaping, sand your bowl, from coarse grit to finer grits, until it feels smooth to the touch. Sanding removes tool marks left from turning, which is crucial before applying the finish. Remember, always wear protection over your nose and mouth during this step because of dust particles that could harm your lungs.
Apply Finish
The last part involves applying a finish, such as oil or wax, which protects the wood and makes its pattern stand out. For my first project, I chose food-safe mineral oil since I planned on using my bowl in kitchen settings. Apply evenly across the entire surface following the manufacturer’s instructions, then let dry completely before final polishing.
Patience is vital throughout all these steps—don’t rush processes, especially when new at-turning bowls.
Benefits of Learning Woodturning Skills
Therapeutic Hobby
Woodturning offers a unique form of relaxation. As you shape wood, the rhythmic sounds and motions can calm your mind. Many find it meditative to watch a rough block transform into something beautiful. This hobby can serve as an escape from daily stress.
I’ve personally felt this therapeutic effect during long sessions at the lathe. The focus required helps clear my thoughts, leaving me refreshed after each project.
Enhancing Skills
Learning woodturning also boosts manual talent and creativity. Handling tools with precision improves hand-eye coordination over time. You’ll learn to visualize designs before making them real.
When I started woodturning, my hands were clumsy, but now they move with purpose and confidence on the lathe.
Financial Avenue
For some, woodturning goes beyond a hobby—it becomes a source of income. Selling bowls or art pieces can turn profitable if done well. It’s satisfying to see others appreciate and pay for your work.
In my early days, I sold a few simple pieces that bolstered my belief in turning passion into profit.
Critical Considerations for New Woodturners
Safety First
Safety is vital in woodturning. Wear protective gear like goggles and a face shield. Ensure your workspace is well-lit and free of clutter. Always check the lathe’s speed before starting. It should match the size of your workpiece.
I always double-check my equipment before turning on the lathe. This habit has saved me from potential accidents more than once.
Choosing the Right Lathe for Your Needs
Budget Consideration
When looking for a lathe, your budget is crucial. Lathes come in various prices. Decide how much you can spend. Then, look at lathes within this range.
Some beginners might opt for a flywheel lathe due to its affordability. I remember starting with a simple model that didn’t break the bank but offered enough features to practice basic strokes.
Space Constraints
Consider the space in your workshop. A giant lathe needs more room but provides greater capacity. Measure your available space before deciding on a lathe size.
A compact treadle or pole lathe could be perfect if you’re tight on space. These types don’t require electricity and are traditional.
Lathe Types
There are different lathes suitable for beginners:
- Spindle lathes: Good for small projects.
- Mini-lathes: Ideal when space is limited.
Choose one based on what you’ll create most often.
My first lathe was a mini-lathe because my workspace was small. It worked well for pens and bowls without overwhelming my shop area.
Purchase Sources
You can buy lathes from hardware stores or online retailers:
- Check product reviews.
- Look at return policies.
Always ask about after-sales support and warranty terms before buying any machine.
Why Woodturning for Beginners?
History Insight
Woodturning has deep roots in history. Dating back to approximately 1300 BC, Ancient Egyptians first pioneered a two-person lathe. One person would operate the treadle to turn the wood, while another used a chisel to cut shapes and flute-like designs into the wood with precise cuts.
I find it fascinating how the craft of woodturning, using traditional tools to create dovetail joints and various shapes, has evolved. From simple bowls and tools, woodturning artists now create complex art pieces using a flywheel lathe or pole lathe and a chisel. This evolution of shapes showcases human innovation at work and our desire to bevel, for example, to shape the world around us.
Safety First
When starting, safety is paramount. Always wear protective gear like goggles and face masks. Ensure your workspace at the center is well-lit and free of clutter to handle any cuts if you need to be careful, especially on your back.
My early days handling the lathe and chisel taught me respect for the machine’s power and the work involved in gouging. I learned quickly that taking precautions with cuts, holding the chisel, and adjusting the angle prevents accidents, allowing me to enjoy my bench work without worry.
Creative Outlet
Woodturning offers immense satisfaction and creativity. Turners use a chisel to transform plain blocks into beautiful objects like small gifts or decorative items. The angle helps them work the material and make precise cuts.
The joy of making something from scratch, working meticulously to cut, gouge, and angle cannot be overstated—it’s why I started wood-turning in the first place! Seeing a workpiece come together as you miss and soak it as envisioned is gratifying.
Basics of the Woodturning Lathe
Lathe Components
A lathe is a vital tool in woodturning. It holds and spins the wood. The main parts of the work include the headstock, tailstock, and tool rest, which are used to cut materials. The headstock has a motor that turns a spindle. This spindle connects to your wood piece.
The tailstock supports the other end of the wood. You can cut and move it to fit different lengths of material for work. The tool rest is where you place your tools to cut while working on spinning wood.
I remember my first time using a lathe at work; learning each part’s role was crucial for safety and skill development. Understanding where to cut was particularly important.
Operating Lathes
Lathes work by spinning wood at high speeds while you cut and shape it with tools like chisels or gouges, such as a spindle gouge, which is perfect for creating detailed patterns in your workpiece.
You control speed or cut it using switches or pedals, much like owning a car’s speed with its accelerator pedal.
In my experience, starting slow helps you gain confidence before moving on to faster speeds, which can be intimidating but necessary for specific cuts.
Common Types
There are several types of lathes used in woodworking:
- Mini lathes are great for small projects like pens or chess pieces requiring precise cuts.
- Midi lathes, ideal for making precise cuts, offer more power and capacity for more oversized items without taking up too much space.
- Full-size lathes are best if you’re serious about large-scale turning projects and must make precise cuts.
Each type of cut suits different needs, but all operate on similar principles involving rotating mechanisms often driven by some flywheel effect, stabilizing rotation during the cut operation.
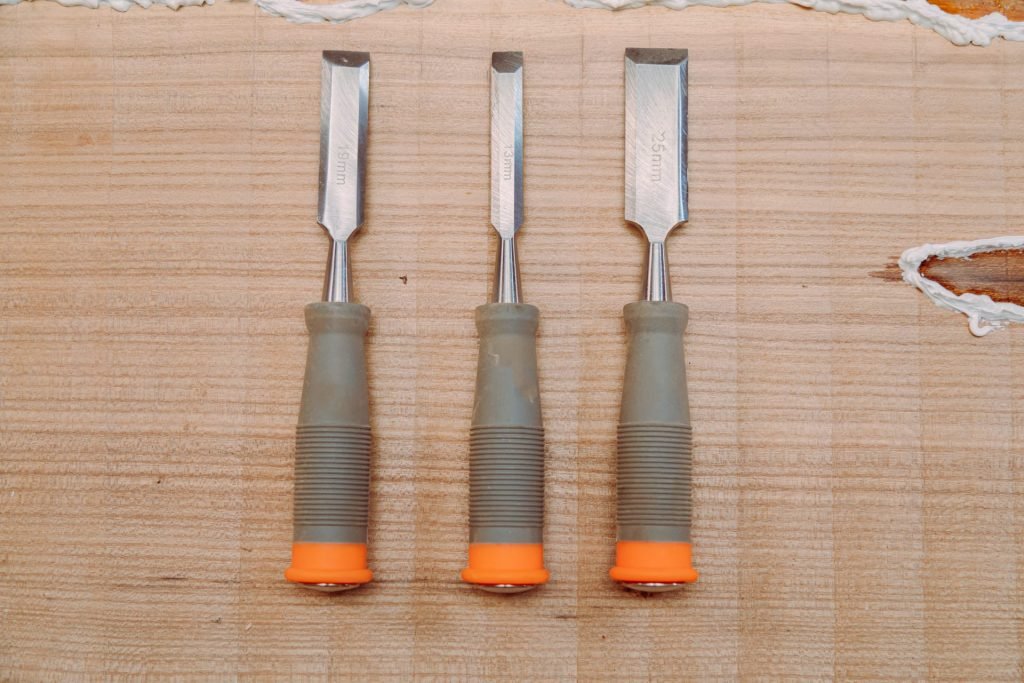
different types of Chisel
Essential Woodturning Tools and Their Uses
Tool Selection
Understanding the tools needed for woodturning is crucial. Beginners must start with a basic set. This includes gouges, skew chisels, parting tools, and scrapers. Each has a unique role in shaping wood.
Gouges help create curves and hollows. Skew chisels are for delicate, smooth cuts on spindles. Parting tools make narrow grooves to separate pieces from the stock. Scrapers smooth out any roughness on the final piece.
Tool Function
The function of each tool is specific to its design. A gouge can carve deep or shallow patterns depending on how it’s angled against the wood. Mastering this angle makes all the difference in my projects.
Skew chisels require precision to avoid digs into your workpiece; they’re great for creating clean lines and details like beads or dovetail joints. Parting tools cut through wood fibers cleanly, which helps when separating finished parts from waste material. Scrapers remove excess material without changing shape, which is ideal for finishing touches.
Maintenance Tips
Proper care extends tool life significantly. Keep them sharp; dull tools can be dangerous and less effective. After using my chisel, I constantly clean it before storing it away — this prevents rust and keeps it ready for next time. Store your tools in a dry place to prevent corrosion. Regularly check handles for cracks or looseness as well; safety first!
Selecting the Right Wood for Turning Projects
Wood Characteristics
When starting a woodturning project, choosing the suitable wood is crucial. It would help if you considered the grain and hardness. Woods with straight grains are more accessible to turn but may be less visually attractive than those with intricate patterns. Hardwoods like maple or cherry are durable and ideal for delicate finishes. Softwoods can be more forgiving for beginners but might not hold details as well.
In my experience, dry wood turns better because it’s less prone to warping or cracking. When I select wood, I always check its moisture content to ensure it’s suitable for hanging.
Sustainable Sourcing
It’s essential to think about where your wood comes from. Try to source sustainable and local materials when possible. This supports local businesses and reduces your carbon footprint due to lower transportation distances.
I often visit nearby sawmills or lumberyards for quality pieces they might consider scrap. This way, I’m recycling what would otherwise go unused while finding some unique pieces of wood that add character to my projects.
Conclusion
Embarking on the woodturning journey, I’ve laid out the essentials to ensure a solid foundation for beginners. From understanding the lathe’s mechanics to mastering basic strokes and selecting suitable wood, these are the building blocks of proficient turning. I’ve shared insights on tools, techniques, and safety—vital knowledge that transforms novices into skilled artisans. My step-by-step guide for crafting your first bowl is a testament to the benefits and satisfaction derived from this craft.
Now it’s your turn at the lathe. Apply these principles, and let your hands create wonders from wood. Remember, practice breeds confidence and skill. So grab your tools, don your safety gear, and start turning! Share your progress with me; I’m eager to see how far you’ll go. Let’s shape something extraordinary together.
Frequently Asked Questions
What is woodturning, and why should beginners consider it?
Woodturning is a form of woodworking where objects are created on a lathe. Beginners should consider it because it allows for creative expression and the development of fine motor skills.
What essential tools do I need to start woodturning?
To start woodturning, you’ll need a lathe, gouges, chisels, a parting tool, a skew chisel, and scrapers. Each plays a crucial role in shaping the wood.
How do I choose the right type of wood for my turning project?
Select woods based on hardness, grain pattern, and color that suit your project’s requirements. Softwoods are more accessible to turn, but hardwoods can provide finer detail.
Can you outline one basic woodturning stroke for beginners?
A fundamental stroke is the ‘bead cut.’ Position your gouge at an angle against the spinning workpiece and gradually shape out semi-circular profiles—ideal for decorative elements.
What safety precautions should new woodturners take?
Always wear safety goggles or face protection. Ensure proper use of sharp tools and follow all guidelines regarding lathe operation to prevent accidents.
Why are learning woodturning skills beneficial?
Learning these skills enhances hand-eye coordination and creativity through design execution in woodworking projects and provides satisfaction from crafting functional art pieces.
How does one select an appropriate lathe as a beginner?
Choose lathes based on size compatibility with your workspace and the types of projects planned; smaller ones suffice for pens, while larger ones accommodate bowls or furniture parts.