Table of Contents
Turning tools for a metal lathe shape and finish metal pieces. They ensure precision and efficiency in machining tasks.
Turning tools are essential in metalworking and machining. They help in shaping, cutting, and finishing metal surfaces with high precision. These tools come in various types, including carbide-tipped, high-speed steel, and ceramic tools. Each type offers unique advantages, such as durability, heat resistance, and sharpness.
Selecting the right turning tool enhances productivity and ensures a smooth machining process. Proper maintenance and handling of these tools are crucial for optimal performance. Investing in high-quality turning tools can significantly impact the quality of the finished product. Understanding the specific needs of your metal lathe can guide you in choosing the most suitable tools.
Introduction To Metal Lathes
Lathes are essential in metalworking. They shape metal parts with precision. Workers use them to cut, sand, and drill metal. Lathes help create tools, parts, and sculptures. They also fix damaged metal parts. Metal lathes make work easier and faster. They are found in factories, workshops, and schools. Lathes come in various sizes and types.
Metal lathes must be strong and durable. They need to handle tough metals. Precision is key for accurate results. Speed control is vital for different tasks. Lathes should have a sturdy base. This helps avoid vibrations. Safety features are also important. They protect workers from accidents. Lathes should be easy to maintain. This ensures long-lasting performance.
Types Of Turning Tools
Turning tools come in various materials. High-speed steel (HSS) is common. It is durable and versatile. Carbide tools are harder and last longer. They are great for precision work. Ceramic tools are used for high-speed operations. They withstand high temperatures. Diamond tools are the hardest. They provide the best finish but are very expensive.
Tool geometry affects performance. The rake angle helps in cutting. A positive rake angle reduces cutting force. A negative rake angle is stronger. The clearance angle prevents rubbing. It ensures the tool does not overheat. The nose radius affects the finish. A larger radius gives a smoother finish. Cutting edge angles also impact the process. They determine how efficient the tool is.
Tool Holders And Inserts
Tool holders keep the cutting inserts in place. They must be tight for safety. Loose holders can cause accidents. Tool holders come in various shapes and sizes. Each one fits a specific job. Always match the holder to the cutting tool.
Quick change holders save time. They allow fast tool swaps. This boosts efficiency in the workshop. Traditional holders need more time to change tools. They require manual adjustments. Quick change is better for busy shops. It reduces downtime.

Credit: waykenrm.com
Tool Selection Criteria
Choosing the right turning tools for a metal lathe involves considering material compatibility, tool durability, and precision. Opt for high-speed steel or carbide-tipped tools for optimal performance. Prioritize tools that maintain sharpness and withstand high temperatures for efficient metalworking.
Material Compatibility
Always choose tools that match the metal you are working with. Steel tools work well for hard metals. Carbide tools are best for tough materials. High-speed steel is great for general-purpose use. Using the right tool prevents damage to both the tool and the workpiece.
Shape And Size Considerations
Tool shape and size should match the lathe operation. Bigger tools are better for heavy cuts. Smaller tools are useful for fine details. Proper tool size ensures accuracy and efficiency. Always select the correct size for your specific task.
Cutting Parameters
Speeds, feeds, and depth of cut are key factors. Cutting speed is the speed of the workpiece surface. It is measured in meters per minute. Feed rate is the distance the tool advances per revolution. This affects the cutting efficiency. Depth of cut is how deep the tool cuts into the material. It influences the strength and finish. Each factor must be adjusted for different materials and tools.
Precision is crucial for metalworking. Small adjustments can make a big difference. Fine-tuning involves tweaking speeds, feeds, and depth of cut. This helps achieve a perfect finish. Consistent monitoring ensures the best results. Regular checks prevent errors and reduce waste. Proper settings extend tool life and improve quality.
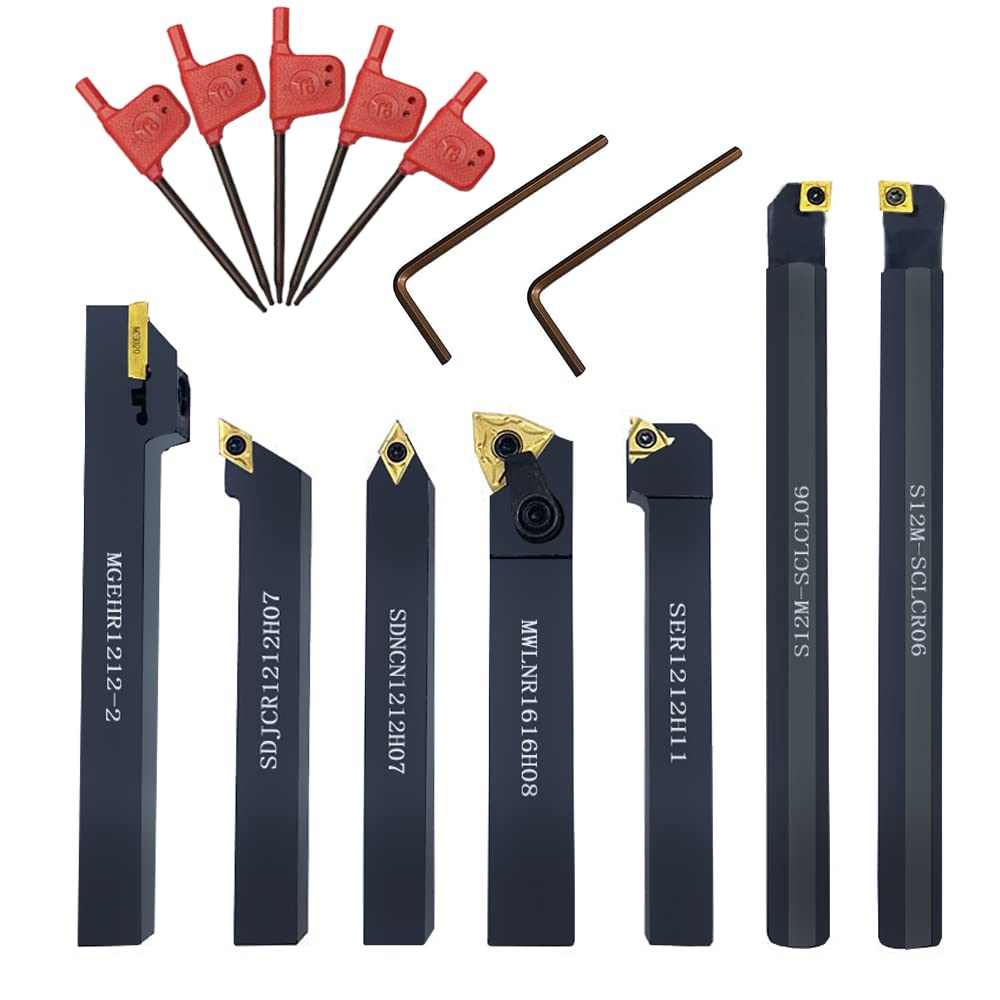
Credit: bigeasymart.com
Sharpening And Maintenance
Keep tools sharp for better performance. Dull tools can damage the metal. Use a grinder to sharpen the tools. Always wear safety glasses when sharpening. Cool the tool often to prevent overheating. Check the tool’s angle and adjust if needed. Use a honing stone for fine edges. Store tools properly to avoid damage.
Look for chips on the cutting edge. Worn tools make rough cuts. Replace tools with cracks or breaks. Inspect tools regularly for wear. New tools cut smoothly and last longer. Keep spare tools ready for quick replacement. Using sharp tools saves time and effort.
Advanced Turning Techniques
Thread cutting is a useful skill. It helps create screws and bolts. Use a threading tool for this task. Set the lathe speed to a low level. Align the tool with the workpiece. Make small cuts to avoid mistakes. Always check the thread pitch. This ensures accuracy. Use cutting fluid to cool the metal. This also helps in getting a smooth finish.
Taper turning creates a cone shape. This is useful for many parts. There are different methods to do this. One way is using the compound rest. Set the angle you need. Another method is offsetting the tailstock. This method is good for long tapers. Always measure your work. Use a dial indicator for accuracy. Make sure to use light cuts. This prevents errors and ensures a smooth surface.
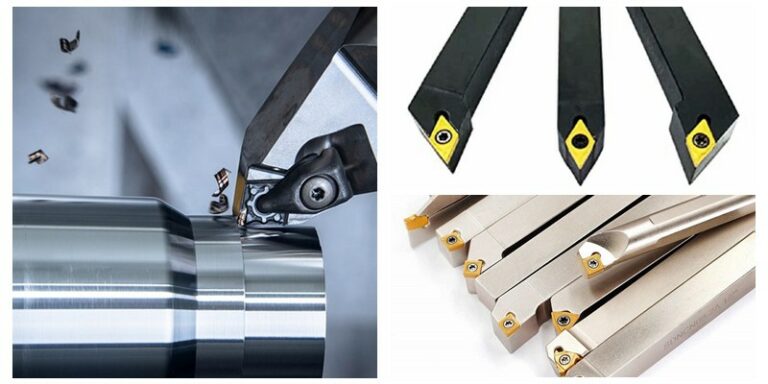
Credit: waykenrm.com
Safety Practices
Ensure safe operation of metal lathes by wearing protective gear. Always secure workpieces and regularly inspect turning tools for damage.
Personal Protective Equipment
Always wear safety glasses to protect your eyes. Gloves should be worn to protect hands from sharp edges. Use ear protection to avoid hearing damage from loud machines. Sturdy shoes can protect your feet from heavy objects. Face shields can offer extra protection for your face.
Machine Safety Features
Machines should have emergency stop buttons. These buttons can stop the machine quickly. Safety guards should cover all moving parts. Guards prevent accidental contact. Machines must have warning signs to alert users. Regular maintenance ensures machines work safely. Maintenance can prevent accidents.
Innovation In Turning Tools
Modern turning tools for metal lathes enhance precision and efficiency in machining. Innovations in materials and design offer improved durability and performance.
Cnc Integration
CNC machines have transformed turning tools. These machines offer precision and efficiency. They can handle complex designs easily. Operators can program them for repetitive tasks. This reduces human error. Speed is another advantage. CNC machines work much faster than manual ones. They also save time and costs. Many industries now rely on CNC turning tools. These tools are essential for modern manufacturing.
Future Materials And Coatings
New materials improve turning tools. Carbide is a popular choice. It is hard and durable. Coatings also play a big role. Titanium nitride is a common coating. It increases tool life. Ceramic materials are becoming popular too. They can handle high temperatures. Diamond coatings are also used. They provide extreme hardness. Future tools will use even better materials. This will make them more efficient.
Frequently Asked Questions
What Are Turning Tools For Metal Lathes?
Turning tools for metal lathes are specialized tools used to shape and cut metal workpieces. They come in various shapes and sizes to perform different functions like cutting, grooving, and threading.
How Do I Choose The Right Turning Tool?
Choose the right turning tool based on the material you’re working with and the required operation. Consider factors like tool geometry, material, and coating to ensure optimal performance.
What Materials Are Turning Tools Made From?
Turning tools are typically made from high-speed steel, carbide, and ceramics. Each material offers different advantages in terms of durability, cutting speed, and precision.
Why Is Tool Geometry Important?
Tool geometry affects the cutting performance, surface finish, and tool life. Proper geometry ensures efficient material removal, reduced tool wear, and better overall results.
Conclusion
Mastering turning tools for a metal lathe enhances precision and efficiency in your projects. With the right tools, you achieve smoother finishes and greater accuracy. Invest in quality tools and practice regularly to refine your skills. Your efforts will result in superior craftsmanship and professional-quality work.
Happy turning!