Table of Contents
A turning tool is a cutting instrument used in metalworking lathes to shape and finish materials. It removes material from a rotating workpiece to achieve desired dimensions.
Turning tools are essential in machining processes. They provide precision and efficiency in shaping various materials. Made from high-speed steel or carbide, these tools can handle different levels of hardness and durability. Operators use them to create smooth finishes, intricate designs, and accurate dimensions.
Proper selection and maintenance of turning tools are crucial for optimal performance. They play a significant role in industries such as automotive, aerospace, and manufacturing. Understanding their functions and applications helps in achieving high-quality results in production.
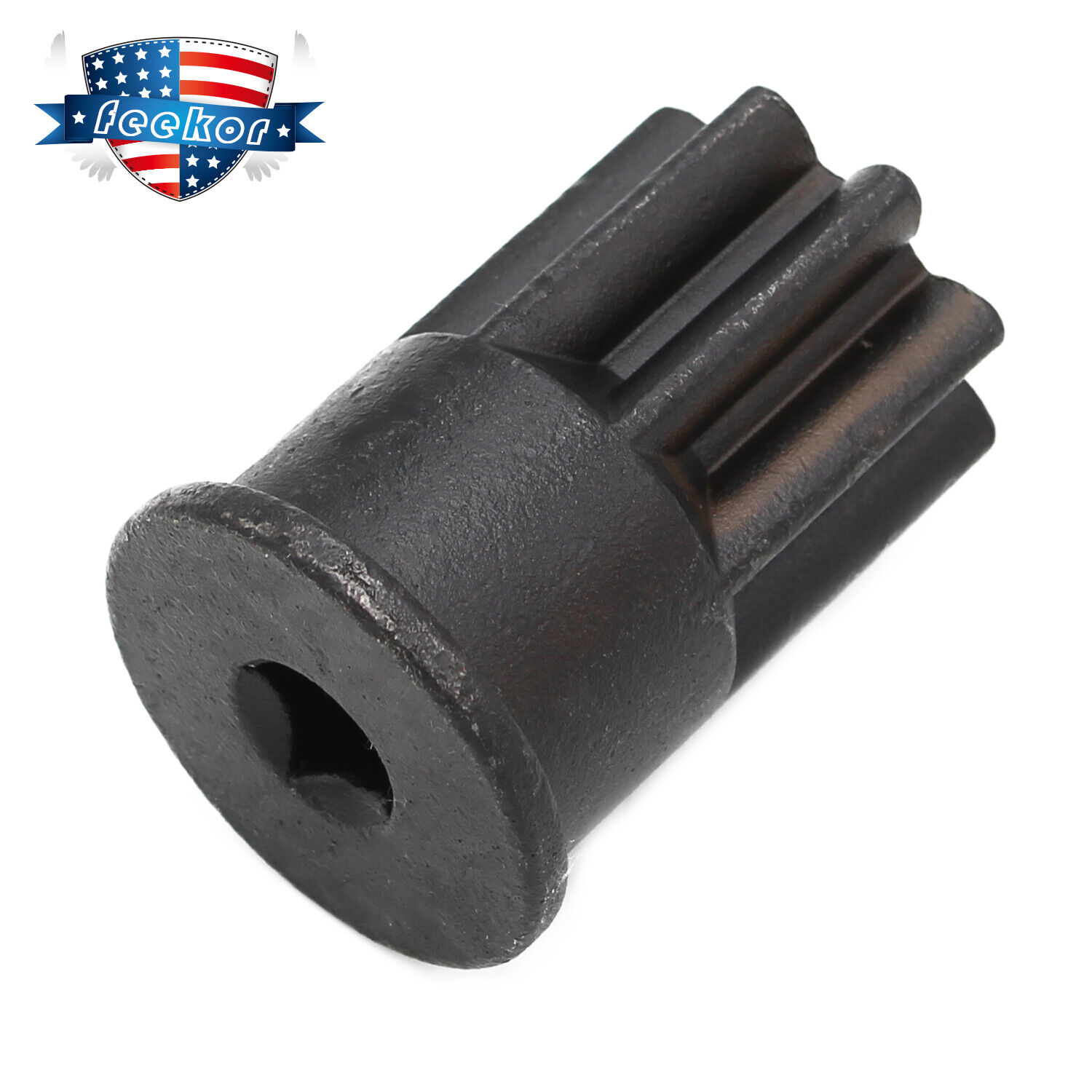
Credit: www.ebay.com
The Essence Of Precision In Lathe Work
Precision is key in lathe work. A small error can ruin a piece. Crafting a perfect item needs a steady hand. Machines help, but skill is crucial. The tiniest detail matters. Every cut must be exact. Measurements should be double-checked. Tools need to be sharp and clean. Proper technique leads to success.
Measuring tools must be calibrated often. Consistent measurements ensure parts fit together. Always use the same tools for each job. This keeps measurements uniform. Small differences can cause big problems. Accurate measurements save time and materials. Consistency helps in creating quality products. Each piece will match the design perfectly.
Selecting The Right Turning Tools
Choosing the right turning tool depends on the material you are working with. For steel, a carbide tool is a great choice. High-speed steel works well for softer metals. Ceramic tools are best for high-speed operations. Each material requires a different tool type for optimal performance.
Turning tools come in various shapes and sizes. Round tools are good for curved surfaces. Square tools provide stability for straight cuts. Triangular tools fit into tight spaces. Choosing the right shape ensures precision and efficiency. Tool size also matters for different projects.
Setting Up For Success
Make sure the workpiece is tightly fixed. Loose workpieces can cause accidents. Use a clamp or vise to hold it. Double-check the grip strength. The workpiece should not move at all. Safety is the top priority.
Position the tool rest close to the workpiece. Keep it within 1/8 inch. Adjust the height to match the tool angle. The tool should touch the workpiece smoothly. Move the tool rest as you work. This ensures better control and precision.
Sharpening Your Tools
Enhance your machining precision by sharpening your turning tool regularly. A sharp tool ensures cleaner cuts and extends tool life. Proper maintenance boosts efficiency in your workshop.
Maintaining The Edge
Keep your tools sharp for better performance. A sharp edge makes cutting easier and safer. Regular maintenance is key. Always check the blade for nicks and dull spots. Use a whetstone or a sharpening tool. Follow the manufacturer’s instructions for best results. Ensure the tool is clean before sharpening. Dirty tools do not sharpen well.
Sharpening Techniques
Start with a coarse grit for very dull edges. Move to finer grits as the edge improves. Use water or oil on the stone to reduce friction. Hold the blade at the correct angle. Keep a steady hand to avoid uneven sharpening. Check the edge frequently. Repeat the process until the blade is sharp.
Mastering Tool Angles
Tool angles are very important. They help in cutting materials. There are three main angles: rake angle, clearance angle, and cutting angle. Each angle has a role. The rake angle controls the cutting force. The clearance angle avoids rubbing. The cutting angle ensures a smooth cut. Knowing these angles helps in better cutting.
Different materials need different angles. Soft materials need a larger rake angle. Hard materials need a smaller rake angle. Cutting speed also matters. Higher speeds need sharper angles. Lower speeds need blunt angles. Choose the right angle for the best result. Adjusting angles improves efficiency and tool life.

Credit: www.amazon.com
The Art Of Cutting Dynamics
Speed is how fast the tool moves. Feed rate is how much the tool cuts per pass. Both are important. They help in making clean cuts. Too fast, and the tool may break. Too slow, and it wastes time.
Choosing the right speed and feed rate is an art. It can change with different materials. A good balance gives the best results. Always start slow and increase speed. This helps in finding the best settings.
Shavings can tell a lot about the cutting process. Thin shavings mean a light cut. Thick shavings mean a heavy cut. Bright and shiny shavings are good. Dark and rough shavings show problems.
Always check the shavings. They help in adjusting the tool. Good shavings mean the tool is working well. Bad shavings mean the tool needs adjustment. Checking shavings can save time and effort.
Avoiding Common Mistakes
Poor finishes can ruin a project. Always ensure the tool is sharp. A dull tool creates rough surfaces. Check the speed of the lathe. Too fast or too slow affects the finish. Use the correct feed rate. Incorrect feed rates lead to poor results. Maintain the proper cutting fluid. It helps in smooth cutting. Clean the work area. Dust and debris can affect the finish. Regularly inspect the machine. Any misalignment impacts the final look.
Tool chatter causes noise and poor cuts. Always tighten the tool post. Loose tools vibrate more. Use a shorter tool length. Longer tools are less stable. Increase the cutting speed. Faster speeds reduce vibrations. Check the tool angle. Incorrect angles cause chatter. Ensure the workpiece is secure. A moving piece will vibrate. Use a heavier tool. Heavier tools absorb more vibration. Regular maintenance is key. Well-maintained machines chatter less.
Advanced Techniques
Intricate detailing requires precision and skill. Use a fine-point tool for tiny details. Keep the tool sharp for clean cuts. Work slowly to avoid mistakes. Steady hands make a big difference. Practice on scrap material first.
Exotic materials need special care. These materials can be hard to cut. Use the right cutting tools to avoid damage. Keep tools cool to prevent overheating. Wear protective gear for safety. Test cuts on small pieces first.
Finishing Touches
Start sanding with coarse-grit sandpaper. This removes rough spots and shapes the wood. Move to medium-grit for a smoother surface. Finish with fine-grit sandpaper for a silky feel. Always sand in the direction of the grain. This prevents scratches and keeps the wood smooth. Clean the dust after each sanding step. Use a damp cloth or vacuum for best results. Sanding prepares the wood for finishes.
Choose the right finish for your project. Options include varnish, oil, and wax. Apply a thin coat with a brush or cloth. Allow it to dry completely. Sand lightly with fine-grit sandpaper between coats. This ensures a smooth and even finish. Repeat the process for multiple coats. More coats provide better protection and shine. Always work in a well-ventilated area. Safety first!
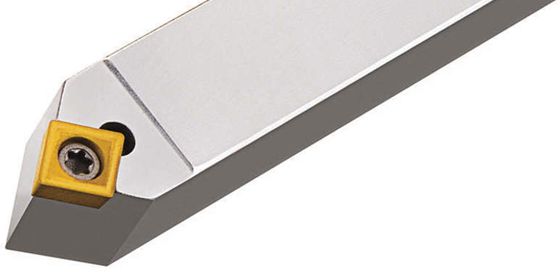
Credit: waykenrm.com
Safety First
Prioritize safety by using proper protective gear when operating a turning tool. Ensure all equipment is well-maintained to avoid accidents.
Personal Protective Equipment
Always wear safety glasses to protect your eyes. Use ear protection to avoid hearing damage. Wear a dust mask to keep dust out of your lungs. Put on gloves to protect your hands. Wear a protective apron to keep your clothes safe. Use steel-toed boots to protect your feet. Make sure your hair is tied back. Avoid loose clothing to prevent accidents.
Lathe Maintenance For Safety
Keep the lathe clean and free of debris. Check the belts for wear and tear. Lubricate all moving parts to reduce friction. Inspect the tools for any damage. Make sure all screws and bolts are tight. Keep the work area well-lit. Ensure the emergency stop button works. Check the electrical connections for safety.
Project Ideas To Inspire
Build a simple pencil holder. Start with a small piece of wood. Use your turning tool to shape it. Create a fun and useful item. Make a wooden spoon. It’s a great first project. Learn how to shape and smooth the wood. Another idea is a wooden ring. It’s easy and quick to make. Give it to a friend as a gift.
Craft a detailed wooden bowl. Requires patience and skill. Add intricate designs. Create a wooden vase. Shape it beautifully with your turning tool. Make a complex chess set. Each piece needs precision. This project can take time. Impress everyone with your skills.
Joining The Community
Forums are great places to meet other turning tool lovers. You can ask questions and share tips. Workshops offer hands-on learning. These events teach you new skills. You can see tools in action. It’s fun to learn with others. You can make new friends. You can share your knowledge too.
Showing your work builds confidence. Take pictures of your projects. Share them online. Use social media to reach more people. Join groups on Facebook or Instagram. People love seeing new ideas. They might give you feedback. This helps you improve. Your work can inspire others. Never be afraid to share.
Frequently Asked Questions
What Is The Name Of A Turning Tool?
The name of a turning tool is a lathe tool. It is used in machining to shape materials.
What Is A Wood Turning Tool Called?
A wood turning tool is called a lathe tool. These tools shape wood on a lathe machine. Common types include gouges, chisels, and skews.
What Is The Name Of The Taper Turning Tool?
The taper turning tool is called a “taper turning attachment. ” This tool is used in lathes for precise taper cuts.
What Is The Most Useful Wood Turning Tool?
The most useful wood turning tool is the bowl gouge. It’s versatile, perfect for shaping and detailing.
Conclusion
Mastering the use of turning tools enhances your craftsmanship and efficiency. These tools are essential for precision and quality. Investing in good turning tools can significantly improve your projects. Start practicing today and see the difference they make. Keep exploring and refining your skills for optimal results.