Table of Contents
Segmented turning involves gluing together multiple pieces of wood to create a blank, which is then turned on a lathe. This technique allows for intricate designs and patterns.
Segmented turning is a fascinating woodworking technique that opens up endless possibilities for creativity. Craftsmen glue together various wood segments to form a blank. This blank is then turned on a lathe to create stunning and intricate designs. Each piece of wood can be chosen for its unique color and grain, resulting in beautiful patterns.
This method is ideal for creating bowls, vases, and other decorative items. The process requires precision and skill, making it a popular choice among experienced woodworkers. With segmented turning, the only limit is your imagination.
Credit: www.finewoodworking.com
The Art Of Segmented Turning
Segmented turning is a unique woodturning technique. It involves gluing multiple pieces of wood. This creates intricate designs and patterns. Ancient craftsmen used solid wood pieces. Segmented turning allows for more creativity and control. Early examples date back to ancient Egypt. Modern turners have refined this art form. Technology has also played a role. Precision tools and machinery have made the process easier. The craft continues to evolve, blending old and new methods.
Traditional woodturning uses a single piece of wood. Segmented turning uses many small pieces. This allows for complex designs. Traditional techniques are simpler but less versatile. Segmented turning offers more artistic freedom. It also uses wood more efficiently. Both methods have their own charm. Each requires a different set of skills. The choice depends on the desired outcome.
Essential Tools And Materials
Master segmented turning with essential tools like a quality lathe, precise calipers, and sharp chisels. Stock up on materials like hardwoods, glue, and clamps for seamless project execution.
Choosing The Right Woods
Different woods bring different qualities. Maple is light and strong. Walnut has a rich, dark color. Cherry offers a warm, reddish hue. Oak is durable and has a distinct grain. Exotic woods like Purpleheart add unique colors. Mixing woods can create striking patterns. Always choose high-quality, dry woods. Wet wood can warp and crack. Avoid soft woods as they are harder to turn.
Must-have Equipment For Segmented Work
A lathe is essential for turning wood. Chisels are used for shaping. Sandpaper smooths the surface. Glue holds the segments together. Clamps keep pieces in place while the glue dries. A bandsaw cuts wood into precise pieces. Measuring tools ensure accuracy. Safety gear like goggles and gloves protect you. Dust collectors keep the workspace clean. A planer can smooth wood before turning.
Design Principles For Segmented Turning
Balance is key in segmented turning. The design should be both beautiful and functional. Each segment must fit together well. This makes the piece strong.
Choosing wood types is important. Different woods offer unique patterns. This adds to the beauty. Colors should complement each other. Too many colors can look messy.
Colors and patterns should work well together. Light and dark woods can create striking contrasts. Patterns should flow naturally. Sharp lines can look harsh.
Repetition of patterns can be pleasing. Too much repetition can be boring. Mix simple patterns with complex ones. This creates interest. Small details can make a big difference.
Preparing Segments For Turning
Crafting precise wood segments is essential for successful segmented turning. Accurate cuts and secure glue joints ensure stability and balance during the turning process. Proper preparation leads to stunning, intricate designs.
Cutting Segments Accurately
Use a sharp saw for clean cuts. Measure each segment carefully. Every piece should fit perfectly. Sand edges to remove splinters. Check the angles with a protractor. Make adjustments if needed. Consistency is key for a smooth turn. Double-check your measurements before cutting. This ensures no mistakes.
Gluing Strategies For Strong Bonds
Apply glue evenly on both surfaces. Use clamps to hold pieces together. Let the glue dry fully. Test the bond by gently pulling. Add more glue if needed. Strong bonds make turning easier. Avoid gaps between segments. They can cause weak spots. Clean excess glue with a damp cloth. This keeps the surface smooth.
Advanced Segmented Patterns
Building complex segmented patterns is fun. Each piece must fit perfectly. Use different wood types for contrast. Start with a simple design. Add more segments as you get better. Keep your tools sharp for clean cuts. Measure each piece carefully. Glue each segment securely. Sand smooth for a nice finish.
Inlays add beauty to your work. Choose a contrasting wood for inlays. Cut the inlay pieces precisely. Fit them snugly into your design. Decorative elements can be added too. Try using metals or stones. Make sure everything is secure. Smooth out any rough edges. Finish with a clear coat for shine.
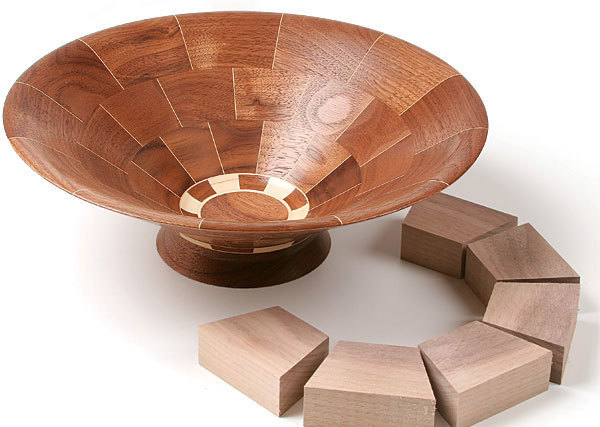
Credit: www.finewoodworking.com
Turning Techniques For Segmented Pieces
Start by securing the segmented blank on the lathe. Use a roughing gouge to shape it. Ensure the blank is balanced before increasing speed. Maintain even pressure to avoid chipping. Gradually refine the shape with a spindle gouge. Keep your tools sharp for clean cuts. Sand the piece with different grits for a smooth finish.
Apply a coat of sanding sealer to the turned piece. Let it dry completely. Sand the piece again with fine-grit sandpaper. Use a tack cloth to remove dust. Apply a finish like lacquer or polyurethane for shine. Let each coat dry before adding another. Buff the piece for a polished look.
Troubleshooting Common Segmented Turning Issues
Check all pieces for proper fit. Make sure edges are smooth and square. Gluing parts together carefully is important. Use clamps to keep pieces in place. Check alignment often during the process. Small gaps can cause big problems later. Sand joints to ensure a perfect fit. Adjust pieces before glue dries.
Use high-quality wood to prevent cracks. Dry wood well before use. Check for knots and weak spots in the wood. Apply glue evenly. Do not over-tighten clamps. Let glue dry completely. Sanding too much can weaken the wood. Handle pieces gently to avoid drops. Store finished pieces in a stable environment.

Credit: www.bucksturners.com
Inspirational Projects To Hone Your Skills
Start with simple segmented bowls. Use basic wood pieces. Glue and sand them together. Make sure to keep the designs easy. Try using a few colors of wood. Practice makes perfect. Patience is key. You will improve fast.
Advanced turners can try intricate vase designs. Use many small segments. Create complex patterns. Experiment with new shapes. Precision is very important. This takes time and skill. The results are worth it. Keep pushing your limits.
Joining The Segmented Turning Community
Many forums offer great tips on segmented turning. You can ask questions and get quick answers. Workshops are also popular. They provide hands-on learning. Experts often lead these workshops. You can learn new techniques. Meeting other woodturners is fun too. Sharing ideas and projects is inspiring.
Competitions are a great way to show your skills. Many woodturners enter these contests. Winning can boost your confidence. Exhibitions are also great for showcasing work. You can meet many talented artists there. It’s a chance to see amazing pieces. You might even sell your work. The community is very supportive.
The Future Of Segmented Turning
Segmented turning has seen many innovations in recent years. New tools make it easier to create precise shapes. Technology has allowed for better designs. Artists now use a wide range of materials. These include exotic woods and even metals. This variety offers more choices for unique projects. Some turners use computer software to plan their pieces. This ensures every segment fits perfectly. These advancements push the boundaries of what is possible.
Woodcraft is moving towards more sustainable practices. Many turners now use recycled or reclaimed wood. This reduces the impact on forests. Eco-friendly finishes are also becoming popular. These finishes are safer for the environment and the user. Some artists choose locally sourced wood. This supports local economies and reduces carbon footprints. Sustainability is now a key focus in the woodcraft community.
Frequently Asked Questions
What Are The Two Types Of Woodturning?
The two types of woodturning are spindle turning and faceplate turning. Spindle turning shapes long, narrow objects like chair legs. Faceplate turning shapes wider, flat objects like bowls and plates.
How To Calculate Segmented Bowl?
To calculate a segmented bowl, measure the diameter, height, and number of segments. Use these measurements to determine the segment angles and dimensions. Use a segmented bowl calculator or formula for precise results.
What Chisel To Use For Wood Turning?
For wood turning, use a spindle gouge, roughing gouge, and parting tool. These are essential chisels for beginners.
What Two Chucks Are Used To Turn Goblets And Cups?
The two chucks used to turn goblets and cups are the four-jaw chuck and the scroll chuck.
Conclusion
Mastering segmented turning can elevate your woodworking projects. This technique offers precision and creativity. Whether you’re a beginner or expert, segmented turning adds unique flair. Dive into this craft, improve your skills, and create stunning pieces. Start experimenting and see the difference it makes in your woodworking journey.
Happy turning!