Table of Contents
Professional metal turning tools are essential for precision machining. These tools ensure smooth and accurate cuts on metal surfaces.
Metal turning tools play a crucial role in the manufacturing and engineering sectors. They are designed to cut and shape metal with high precision. This precision is vital for producing intricate components and maintaining tight tolerances. High-quality tools enhance productivity and reduce downtime by maintaining their sharpness longer.
They include a variety of cutting instruments like lathes, chisels, and rotary cutters. Each tool serves a specific purpose, enabling machinists to achieve desired shapes and finishes. Investing in professional-grade metal turning tools ensures durability, efficiency, and superior performance. Quality tools translate to high-quality end products, making them indispensable in any metalworking shop.
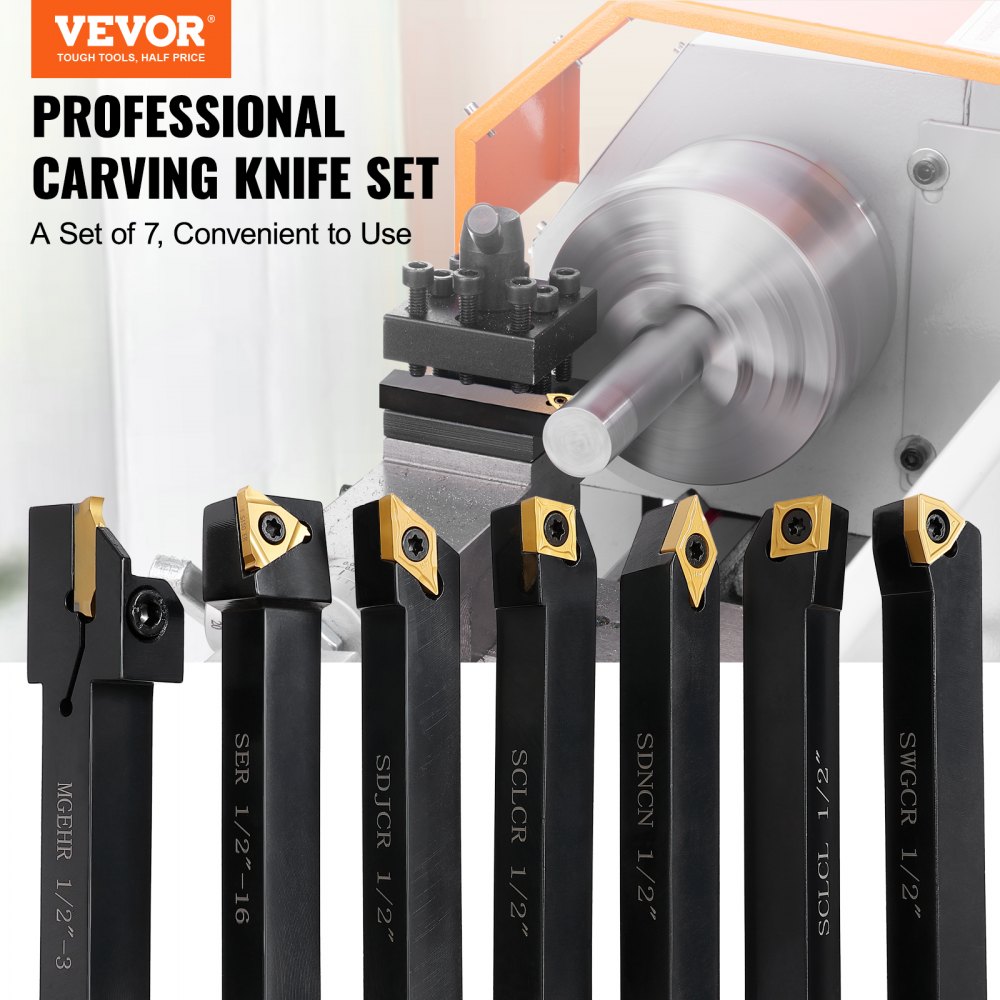
Credit: www.vevor.com
Introduction To Metal Turning Tools
Metal turning tools are very important for making things with metal. They help shape and cut metal into the right form. Craftsmen use these tools to make items like car parts and jewelry. Tools need to be strong to cut through hard metals. Precision is key, so the tools must be sharp and well-made.
Accurate machining is important in metalwork. Metal turning tools help achieve this. They allow for precise cuts and shapes. Using the right tool ensures the final product fits perfectly. This is crucial in industries like aerospace and automotive. Accuracy saves time and reduces waste. Well-made tools make the job easier and more efficient.
Types Of Metal Turning Tools
Roughing tools remove large amounts of metal quickly. They are strong and can take heavy cuts. Finishing tools create a smooth surface on the metal. They are precise and make small cuts. Both tools are important in metal turning.
Boring bars help create precise holes. Threading tools cut threads for screws and bolts. Grooving tools make grooves in the metal. Each tool has a special job. Using the right tool makes the work easier and faster.
Materials Used In Tool Construction
Professional metal turning tools often utilize materials like high-speed steel, carbide, and ceramics. These materials ensure durability, precision, and efficiency in machining operations.
Carbide Inserts
Carbide inserts are very strong. These inserts resist wear and heat. They cut metals easily. Carbide inserts are used in many industries. These inserts last longer than steel tools. They are very sharp.
High-speed Steel And Beyond
High-speed steel (HSS) tools are also used. HSS tools are less expensive. They are not as hard as carbide. HSS tools are good for soft metals. New materials are being tested. These materials may work better than HSS. Some tools use ceramic or diamond tips. These tips can cut very hard metals. Each material has its own use.
Design Features For Enhanced Performance
The cutting edge geometry is critical for high precision. It helps in improving the surface finish. The shape of the cutting edge reduces cutting forces. This leads to better tool life and efficiency. Proper geometry can reduce heat buildup. This is important for maintaining tool integrity.
Toolholders play a key role in securing the cutting tool. They offer better stability and minimize vibrations. New designs include quick-change mechanisms. These allow for faster tool changes. Some toolholders have coolant channels. This helps in cooling the cutting area. Improved clamping systems provide greater accuracy.
Tool Selection For Different Metals
Choosing the right tool for different metals is crucial. Stainless steel needs hard tools. Aluminum needs softer tools. For stainless steel, carbide tools work best. For aluminum, high-speed steel is ideal. Each metal has unique needs. Using the right tool prevents damage. It also ensures a smooth finish.
Tool coatings improve performance. Titanium nitride is a common coating. It works well with steel. Diamond-like coatings are great for aluminum. Choosing the right coating extends tool life. It also makes cuts cleaner and more accurate. Matching the coating to the metal enhances efficiency.
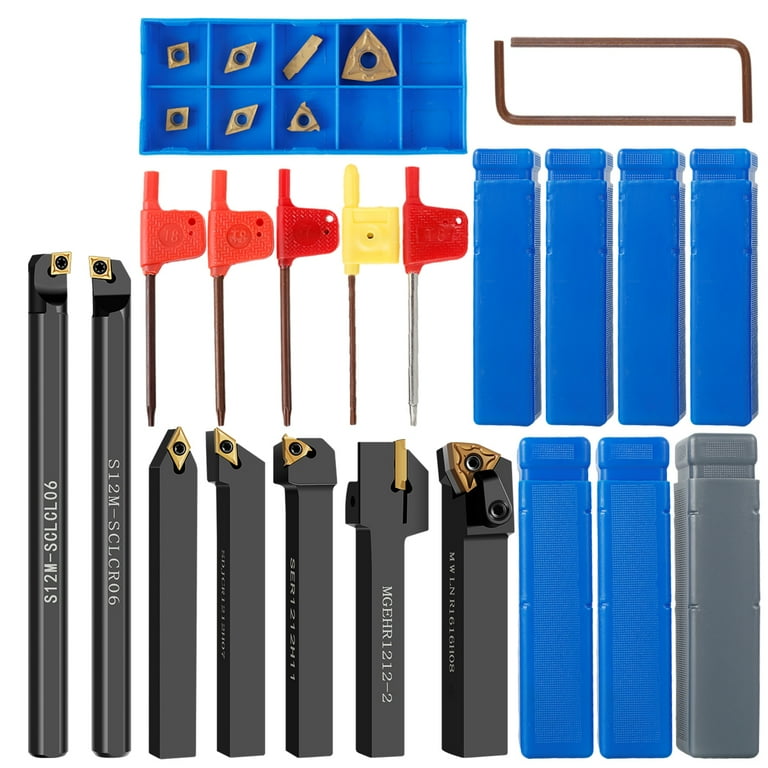
Credit: www.walmart.com
Precision Engineering In Tool Manufacturing
Precision engineering ensures tools meet strict tolerances. This improves the tool life. Every tool must fit perfectly to work well. Slight differences can cause big problems. Tools with good tolerances last longer. They also provide better results. Engineers measure every part carefully. This attention to detail makes a big difference. Professionals rely on these tools for their work. Durability and accuracy go hand in hand. High standards lead to better performance.
Quality assurance checks are important. They ensure each tool is perfect. Every step gets monitored closely. Tests are done to check strength and durability. Tools must pass all tests before use. This keeps them reliable. Quality checks catch any flaws early. This saves time and money. Reliable tools mean fewer problems. Workers trust tools that are well-made. This trust is built through good quality control.
Maintaining Tools For Longevity
Proper care ensures professional metal turning tools remain sharp and effective. Regular cleaning and lubrication prevent rust and wear. Store tools in a dry place to extend their lifespan.
Proper Storage Practices
Keep tools in a dry place to prevent rust. Use toolboxes with compartments for better organization. Hanging tools on a pegboard can save space and keep them visible. Always clean tools before storing them. Avoid storing tools in damp areas like basements. Labeling helps you find tools faster. For small parts, use containers or jars.
Sharpening And Care Techniques
Sharpen tools with a grinding wheel or stone. Always follow the manufacturer’s guidelines. Keep the blade angle consistent while sharpening. Use a lubricant to reduce friction. Wipe tools after use to remove debris. Regularly inspect tools for wear and tear. Replace parts if they are damaged. Use a protective coating to prevent rust. Store sharpened tools safely to avoid accidents.
Technological Advancements In Metal Turning
CNC machines are changing metal turning. These machines are very precise and fast. They use computer controls to shape metal. This makes the process more efficient. Errors are rare with CNC machines. Human work is now easier. Metal parts are made faster. Costs are lower too. CNC technology is the future of metal turning.
New materials are being used in tools. Carbide and ceramics are popular. They last longer and cut better. These materials are also very strong. They can handle high temperatures. This is important for metal turning. Coated tools are also in demand. Coatings make tools even more durable. They prevent wear and tear. The future looks bright for metal turning tools.
Case Studies
Explore case studies showcasing the efficiency and precision of professional metal turning tools. These real-world examples highlight significant improvements in manufacturing processes and product quality.
Real-world Applications
A company used metal turning tools to create aircraft parts. The tools helped achieve high precision. The parts fit perfectly in the engines. This improved the safety of the aircraft.
Another company used these tools for car manufacturing. The tools made custom parts quickly. This saved time and money. The cars were more reliable and efficient.
Success Stories In Precision Metal Turning
An engineer used metal turning tools for medical devices. The tools crafted tiny parts. These parts were crucial for surgeries. Lives were saved due to the high quality of the devices.
A small business owner used these tools for custom jewelry. The tools allowed fine detailing. Customers loved the unique designs. The business grew rapidly with happy customers.

Credit: www.amazon.com
Safety Considerations And Best Practices
Always wear safety goggles to protect your eyes from metal chips. Gloves are important to keep your hands safe. A face shield can offer extra protection. Ear protection helps guard against loud noises. Steel-toed boots keep your feet safe from heavy objects. Aprons can protect your clothing and skin from hot metal.
Inspect the machine before use. Make sure all parts are in good condition. Secure your workpiece properly. Always use the right tool for the job. Keep your hands away from moving parts. Never leave the machine running unattended. Turn off the machine after use. Keep your workspace clean and free from clutter.
Choosing The Right Supplier
Always check the supplier’s reputation. Happy customers often mean good service. Look for suppliers with quality certifications. This ensures you get the best tools. Prices should be competitive but not too cheap. Cheap often means low quality.
Customer service is very important. Quick responses show they care. Check if they offer warranties. A good warranty means they trust their tools. Finally, see if they have a wide range of products. More options can be helpful.
Start by communicating clearly. Tell them your needs and expectations. Regular contact builds trust. Always pay on time. This shows you are reliable. Visit their facility if possible. This helps you understand their operations.
Share feedback with them. This helps them improve. A good relationship benefits both sides. Always be respectful and professional. This goes a long way. Remember, a strong partnership is key to success.
Frequently Asked Questions
What Is The Best Metal For Lathe Tools?
High-speed steel (HSS) is the best metal for lathe tools. It offers durability, sharpness, and heat resistance.
What Is The Most Versatile Turning Tool?
The most versatile turning tool is the carbide insert tool. It offers durability, precision, and compatibility with various materials.
What Are The Three Types Of Lathe Tools?
The three types of lathe tools are turning tools, boring tools, and threading tools. These tools shape, enlarge, and thread materials.
How Do I Choose A Turning Tool?
Choose a turning tool based on material, tool geometry, cutting speed, feed rate, and surface finish requirements. Ensure compatibility with your machine.
Conclusion
Choosing the right metal turning tools can significantly enhance your machining projects. High-quality tools ensure precision and durability. Investing in professional equipment not only boosts efficiency but also extends the life of your machinery. Stay ahead in your industry by opting for reliable metal turning tools.
Your projects deserve the best.