Table of Contents
Metalworking turning is a machining process that uses a cutting tool to remove material from a rotating workpiece. It creates cylindrical parts with precision.
Metalworking turning is essential in manufacturing industries. It involves securing a workpiece on a lathe and rotating it while a cutting tool shapes it. This process allows the creation of precise, cylindrical components used in various applications, from automotive to aerospace.
The turning process enhances surface finish and dimensional accuracy, making it ideal for producing intricate parts. Different types of lathes, such as CNC and manual, cater to various production needs. Mastery of turning techniques and understanding tool selection are crucial for achieving optimal results in metalworking. Investing in quality equipment and skilled operators ensures high productivity and efficiency.
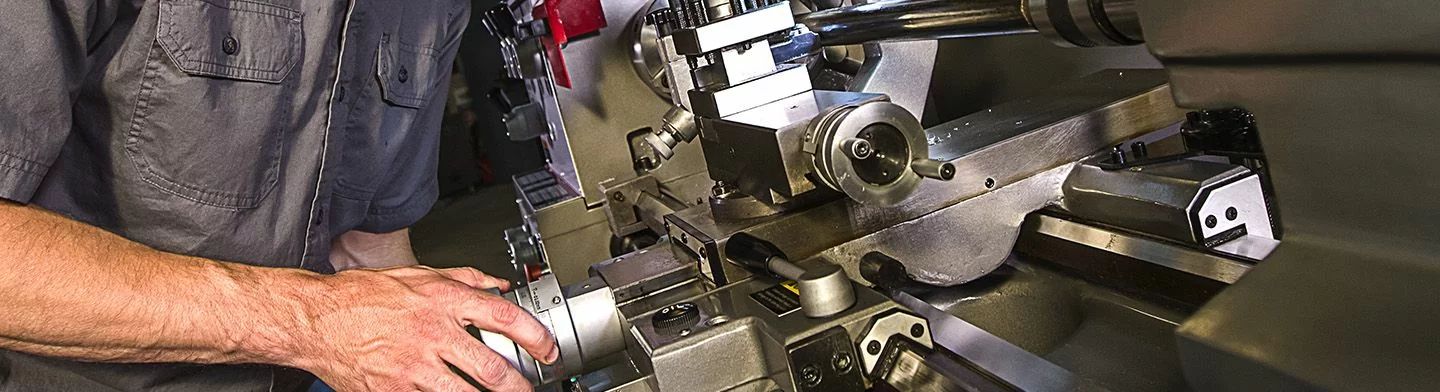
Credit: jettools.com
Introduction To Metalworking Turning
Metalworking turning involves rotating a metal piece while a cutting tool shapes it. This process creates precise cylindrical parts essential in various industries.
The Basics Of Turning
Turning is a metalworking process. It involves removing material from a rotating workpiece. A cutting tool is used to achieve this. The tool moves in a linear path. This process creates cylindrical parts. Turning is done on a machine called a lathe. There are different types of lathes. Some are manual, and some are automated. Basic turning operations include facing, threading, and parting. Each operation serves a specific purpose. Accuracy and precision are crucial in turning.
Evolution Of Turning Techniques
Turning techniques have evolved over time. Early lathes were simple and hand-operated. Modern lathes are highly advanced. They use computer numerical control (CNC) technology. CNC lathes offer greater precision and automation. This reduces human error. They can perform complex operations with ease. The materials used in turning have also changed. Initially, only soft metals were used. Now, turning can be done on hard metals and composites. This makes the process versatile and efficient.
Types Of Turning Operations
Facing is a crucial turning operation. It creates a flat surface on the end of a workpiece. This process is often the first step in machining. The tool moves perpendicularly to the workpiece’s axis. Precision is key in facing for a smooth finish.
Taper turning produces a conical shape on a workpiece. This is done by gradually reducing the diameter. The lathe tool moves at an angle to the workpiece axis. Taper turning is essential for parts that need a precise fit.
Thread cutting creates screw threads on a workpiece. This operation is vital for fasteners like bolts and screws. The tool follows a helical path along the workpiece. Accurate thread cutting ensures parts fit together securely.
Selecting The Right Tools
Choosing the correct tool material is crucial. High-speed steel (HSS) is popular for its toughness. Carbide tools offer longer life and faster cutting speeds. Ceramic tools are great for high-temperature applications. Cubic boron nitride (CBN) excels in cutting hard materials. Each material has its specific benefits.
Tool geometry affects the cutting process. Rake angle influences the cutting forces. A positive rake angle reduces power consumption. Clearance angle prevents the tool from rubbing against the workpiece. Nose radius affects the surface finish. Larger nose radius provides a smoother finish. Each angle and radius is important.
Coatings can extend tool life. Titanium Nitride (TiN) is a common coating. It reduces friction and wear. Titanium Carbonitride (TiCN) offers better hardness. Aluminum Oxide (Al2O3) is ideal for high-speed applications. Diamond coatings are used for non-ferrous materials. Treatments enhance tool performance.

Credit: elemetgroup.com
Setting Up The Lathe For Precision
Calibration ensures accurate measurements. Always check the lathe’s settings. Adjust dials to zero. Confirm the machine is level. Use a spirit level for best results. Regular checks prevent errors.
Secure the workpiece tightly. Use a chuck or faceplate. Ensure it is centered. Off-center workpieces cause problems. Double-check the grip. Loose pieces can be dangerous.
Align tools with the spindle. Use a dial indicator. Ensure the tool is at the correct height. Incorrect alignment affects the cut. Always tighten the tool post. Loose tools can shift.
Advanced Turning Techniques
High-speed turning uses very fast cutting speeds. This reduces machining time. The process improves surface finish. It also extends tool life. Special machine tools and cutting inserts are needed. High-speed turning is common in aerospace and automotive industries.
Hard turning is used for very hard materials. The hardness is usually above 45 HRC. This technique replaces grinding in some cases. It uses ceramic or CBN tools. Hard turning is efficient for small batches. It reduces setup time and cost.
Micro turning creates very small parts. It uses micrometer precision. This technique is important for medical devices. Micro turning also serves electronics and watchmaking. Tools and machines must be very accurate. Small errors can ruin the parts.
Optimizing Feed Rate And Speed
Use formulas to find the best feed rate and speed. Consider the material hardness and tool type. Always check manufacturer guidelines. Adjust rates based on these factors.
Different materials need different settings. Soft materials require higher speeds. Hard materials need slower speeds. This prevents tool damage. Always test on a small piece first.
Regularly inspect your tools. Look for signs of wear like dull edges. Replace tools when worn out. Sharp tools work better and last longer. Keep your tools in good condition.
Troubleshooting Common Turning Issues
Poor surface finish can be a common issue. Check if the cutting tool is sharp. Dull tools create rough surfaces. Feed rate and cutting speed also affect the finish. High feed rates can cause roughness. Adjust these settings to improve the finish. Use coolant to reduce heat and improve surface quality.
Tool life is important in turning. Cutting speed plays a big role. High speeds wear out tools fast. Use the right material for your tools. Harder materials last longer. Coolant helps to extend tool life. It reduces heat and friction. Regular maintenance keeps tools in good shape.
Accurate workpieces are crucial. Machine calibration is key. Check your machine settings often. Tool wear affects accuracy. Replace worn tools promptly. Workpiece material also matters. Softer materials may deform. Use proper clamping to secure the workpiece. This prevents movement and ensures precision.
Mastering Precision Through Practice
Start with simple turning exercises. Use a lathe for basic shapes. Make sure you practice straight cuts. Try to create cylindrical shapes. Move on to tapered cuts next. Finish with complex shapes.
Check the smoothness of the surface. Measure the diameter with calipers. Look for symmetry in your work. Ensure there are no rough edges. Compare your outcomes with standard measurements.
Keep a logbook of your progress. Write down errors and successes. Set new goals every week. Study advanced techniques from experts. Practice regularly to build confidence.

Credit: cncpartsxtj.com
Frequently Asked Questions
What Is Turning In Metal Work?
Turning in metal work is a machining process. It involves rotating the workpiece while a cutting tool removes material, shaping it to the desired form. This technique is essential for creating cylindrical parts and achieving precise dimensions.
What Is The Working Process Of Turning?
Turning involves rotating a workpiece while a cutting tool removes material to shape it. The tool moves linearly. This process creates cylindrical parts and precise dimensions. It’s commonly used in manufacturing industries.
What Are The 5 Main Parts Of A Metal Turning Lathe?
The five main parts of a metal turning lathe are the bed, headstock, tailstock, carriage, and lead screw.
How Many Types Of Turning Are There?
There are several types of turning, including straight turning, taper turning, contour turning, and form turning. Each type addresses specific machining needs and shapes.
Conclusion
Mastering metalworking turning can elevate your craftsmanship. Stay updated with techniques and tools for optimal results. Remember, practice leads to perfection in metalworking. Keep honing your skills and explore new methods. Enjoy the art of turning and create exceptional metal pieces.