Table of Contents
Metal turning segments are essential components in machining processes, offering precision and efficiency. They shape and finish metal parts with accuracy.
Metal turning segments play a vital role in manufacturing and engineering. These components are used to cut, shape, and finish metal parts with high precision. Metal turning segments ensure that the final product meets exact specifications, enhancing overall quality. They are commonly used in industries such as automotive, aerospace, and machinery.
The use of metal turning segments increases productivity and reduces waste, making them indispensable in modern machining. Choosing the right metal turning segment can significantly impact the efficiency and outcome of your project. Quality segments contribute to smoother operations and longer tool life, optimizing the entire manufacturing process.
Introduction To Metal Turning Segments
Metal turning segments are crucial in precision engineering. They help shape metal parts with great accuracy. Precision is important for making machines work well. Metal turning ensures each part fits perfectly. This helps machines run smoothly and last longer.
Engineers rely on these segments for high-quality results. Precise metal parts reduce wear and tear. They also improve performance and efficiency. Quality control is easier with precise segments. This makes engineering projects more successful.
Metal turning has evolved a lot over the years. Early methods were manual and slow. Today, we use advanced machines for metal turning. These machines are faster and more accurate. Technology has greatly improved metal turning practices.
Computer Numerical Control (CNC) machines are now common. They automate the metal turning process. CNC machines are precise and reliable. They make it easier to produce complex parts. Modern metal turning is more efficient and effective.
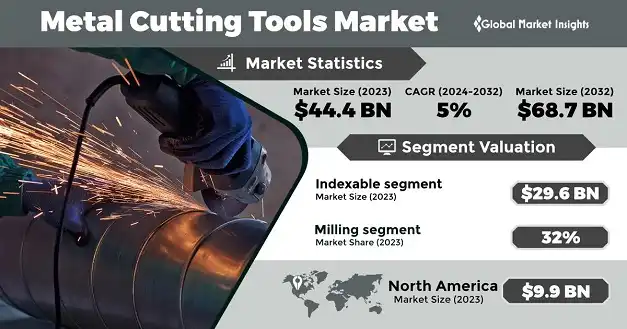
Credit: www.gminsights.com
Key Elements Of Metal Turning
Lathes are machines that help shape metal. They spin the metal around quickly. A sharp tool cuts the metal. The main parts of a lathe include the bed, headstock, and tailstock. The bed holds everything together. The headstock spins the metal. The tailstock supports the metal from the other end. A carriage moves the cutting tool to shape the metal. Lathes can be manual or automatic. Manual lathes need a person to control them. Automatic lathes work by themselves.
Different metals need different tools. Steel is tough and needs strong cutting tools. Aluminum is softer and easier to shape. Brass is good for detailed work. Each metal has its own best speed for cutting. Cutting too fast can damage the tool. Cutting too slow can take too long. Using the right tool and speed makes metal turning easier.
Advancements In Turning Technology
CNC machines have changed metal turning. They are very precise. These machines make parts exactly the same every time. This reduces mistakes. It saves time and money.
Factories use CNC machines for big jobs. They can run all day and night. Workers do not need to watch them all the time. This helps make more parts faster. Parts made by CNC machines fit together better.
New tools make metal turning easier. Special coatings on tools help them last longer. They cut metal faster and stay sharp. This means less time changing tools.
New equipment is also smarter. Machines can now check their own work. They find mistakes before they become big problems. This makes sure every part is perfect. Factories can make many parts without stopping.
Materials And Alloys: Shaping The Future
New materials are changing metal turning. Graphene and nanocomposites are some of these materials. They are very strong and light. This helps in creating better metal parts. Titanium alloys are also becoming popular. They are used in aerospace and medical industries. Ceramic materials are also being explored. These materials can handle high temperatures. They are also resistant to wear and tear. Innovative materials are making metal turning more efficient.
Advanced alloys are improving performance in metal turning. Superalloys can withstand high stress and temperature. These are used in jet engines and power plants. Aluminum alloys are lightweight and strong. They are ideal for automobile and aerospace applications. Copper alloys offer excellent conductivity. They are used in electrical and thermal systems. Steel alloys remain popular. They offer a good balance of strength and flexibility. Each alloy has unique benefits.
Precision Engineering Applications
Metal turning segments play a vital role in aerospace and aviation. They ensure parts are made with high precision. This precision is crucial for safety and performance. Planes and spacecraft rely on these parts to function properly. High-quality materials are used to withstand extreme conditions. Precision engineering helps in creating complex components needed for flight.
The automotive industry benefits greatly from metal turning segments. These segments help in producing engine parts and transmission systems. Precision is key to ensure vehicles run smoothly and efficiently. Fuel efficiency and performance are enhanced with well-crafted parts. Metal turning enables mass production of high-quality components. This leads to reliable and durable vehicles on the road.
Quality Control In Metal Turning
Precise measuring techniques ensure high-quality metal turning. Tools like calipers and micrometers are essential. These instruments measure dimensions accurately. They help maintain tight tolerances. Optical comparators are also used. These devices visualize the part’s profile. It helps in comparing against standard templates. Laser measuring systems are modern tools. They offer high precision and speed.
Maintaining tight tolerances is crucial in high-volume production. Automated systems enhance consistency. They reduce human error. CNC machines are commonly used. These machines offer precision and repeatability. Regular calibration of equipment is necessary. This ensures accuracy over time. Quality checks at each stage help. They catch defects early in the process.
Economic And Environmental Considerations
Metal turning can save money. Machines work fast and use less power. Less waste means less cost for materials. Automated tools need fewer workers. This reduces labor costs. Quality control is easier with machines. Better quality means fewer mistakes. Fewer mistakes save money too.
Using recycled metal is good for the Earth. Less mining means less damage to nature. Machines can be eco-friendly. They use less power and create less waste. Coolants can be recycled too. This saves water and keeps it clean. Smart planning helps to use every bit of metal. This reduces waste and helps the planet.
Future Trends In Metal Turning Segments
Predictive maintenance uses sensors and data to predict machinery failures. This helps reduce downtime and saves costs. Machines can be fixed before they break. Real-time monitoring is key to this process. It ensures machines run smoothly. Data collected helps in planning maintenance schedules. This leads to better resource management.
AI and robotics are changing the metal turning industry. Robots can perform tasks with high precision. AI helps in decision-making processes. This improves efficiency and reduces human error. Robots work continuously without fatigue. AI systems analyze data for improved operations. Automation in metal turning leads to higher productivity. It also ensures consistent quality in production.
Conclusion: The Impact On Modern Manufacturing
Metal turning has changed how we make things. Machines now cut metal with great precision. This leads to better products and less waste. Many industries benefit from this technology. It saves time and money. Metal turning is now a key part of manufacturing.
Precision engineering will keep growing. New tools and techniques will emerge. This will make metal turning even more efficient. Factories will use these tools to make high-quality products. Innovation will drive this field forward. Many young people will choose careers in this area.

Credit: en.wikipedia.org

Credit: www.researchgate.net
Frequently Asked Questions
What Is The Process Of Turning Metal?
Turning metal involves using a lathe. The lathe rotates the metal while a cutting tool shapes it. This process can create cylindrical parts, threads, and more. Proper speed and feed rates are crucial for precision.
What Is The Easiest Metal To Lathe?
Aluminum is the easiest metal to lathe. It is soft, malleable, and generates less heat during machining.
What Are Metal Turning Segments?
Metal turning segments are parts of a workpiece removed during the turning process. They help shape the final product.
Why Are Metal Turning Segments Important?
Metal turning segments are crucial for precision machining. They ensure the workpiece meets exact specifications and desired shapes.
Conclusion
Understanding metal turning segments enhances productivity and precision. Adopting the right techniques ensures superior quality and efficiency. Stay informed and leverage these insights for optimal outcomes in your metalworking projects. Keep refining your skills and embrace advancements for continued success in the industry.