Table of Contents
Metal turning lathe tools are essential for shaping metal workpieces on a lathe. They cut, shape, and finish metals efficiently.
Metal turning lathe tools play a crucial role in machining operations. They help in cutting, shaping, and finishing metal workpieces with precision. These tools come in various types, including carbide-tipped, high-speed steel, and diamond-tipped tools. Each type has its specific use, depending on the material and desired finish.
Proper selection and maintenance of lathe tools ensure optimal performance and longevity. Regular sharpening and correct handling can significantly enhance productivity. Investing in quality lathe tools can lead to better accuracy and efficiency in metalworking projects. Understanding their applications and maintenance needs is vital for achieving the best results in metal machining.
Introduction To Metal Turning Lathe Tools
Metal turning lathe tools are used to shape metal. They are vital in metalworking. Precision is key to their effectiveness. Tools must be sharp and well-maintained. Proper usage ensures smooth and accurate cuts. Different tools serve different purposes.
- Cutting Tools: Cut and shape metal pieces
- Boring Bars: Enlarge holes in metal
- Parting Tools: Cut off parts of the workpiece
- Threading Tools: Create threads on metal
- Turning Tools: Shape the outer surface
Precision in metal turning ensures high-quality results. Accurate measurements are crucial. Tiny errors can ruin the piece. Tools must be positioned correctly. Skilled operators can achieve perfect cuts. Always double-check settings for best outcomes.
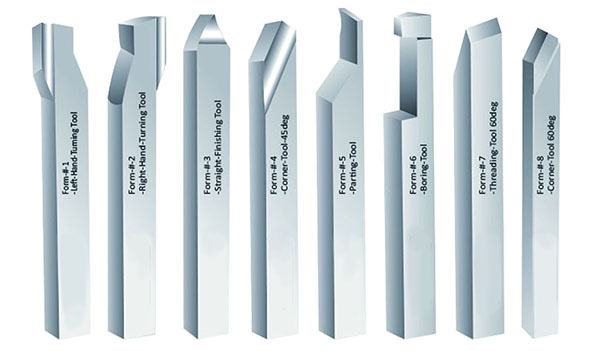
Credit: www.penntoolco.com
Types Of Metal Turning Lathe Tools
Cutting tools are essential in metal turning. They are made from high-speed steel or carbide. High-speed steel is tough and lasts long. Carbide tools stay sharp longer. The geometry of the tool is also important. The shape and angle affect the cutting. A good tool makes clean cuts. Proper material and geometry ensure smooth work.
Supporting tools help keep accuracy high. Calipers measure the diameter of the workpiece. Dial indicators check the alignment. Tool holders keep the tools steady. Chucks and collets hold the workpiece firmly. Each tool helps in making precise cuts. Accuracy is key in metal turning.
Materials Used In Lathe Tool Construction
High-Speed Steel (HSS) tools are very strong and durable. They can cut through many metals. Carbide tools are even tougher. Carbide tools stay sharp for a long time. HSS tools are cheaper but wear out faster. Carbide tools cost more but last longer. Both types have their own uses.
Cobalt tools are very hard and can cut faster. They are good for heavy-duty work. Ceramic tools are even harder. They can cut at very high speeds. Cobalt tools resist heat well. Ceramic tools stay sharp longer. Both types help in high-speed cutting.

Credit: www.pinterest.com
Tool Holders And Inserts
Tool holders keep the cutting tools in place. They ensure accuracy and stability. Proper securing is important for smooth operation. Misalignment can cause errors and damage. Always check the alignment before use. Use the right tool holder for each job.
Quick change systems save time. They make switching tools fast and easy. This system helps improve workflow. No need to stop the machine for long. It helps in maintaining efficiency. Always ensure tools are secure in the quick change holder.
Lathe Tool Geometry
Angles play a key role in cutting. A small rake angle can improve strength. Large rake angles can reduce cutting force. Relief angles help in preventing tool wear. Positive relief angles are common. Side cutting edge angle affects chip flow. A larger angle can improve surface finish. Different angles suit different materials.
Tool nose radius affects surface finish. A small radius produces a fine finish. A larger radius increases tool strength. Larger radii are better for rough cuts. Smaller radii suit finishing cuts. The nose radius also impacts vibration. Larger radii can reduce tool chatter.
Sharpening And Maintenance Of Lathe Tools
Always keep your lathe tools sharp. Use a grinding wheel to sharpen. Maintain the correct angle for each tool. Use a coolant to prevent overheating. Regular sharpening extends tool life. Do not press too hard while grinding. Check the tool’s edge often. A dull tool damages the workpiece. Sharpening should be consistent.
Clean your tools after every use. Lubricate moving parts to reduce wear. Store tools in a dry place. Inspect tools for damage regularly. Replace worn-out parts quickly. Proper storage prevents rust. Use a tool holder for safe storage. Handle tools with care. Avoid dropping them. Good maintenance ensures long tool life.
Setting Up Lathe Tools For Precision Work
Proper alignment of lathe tools is vital for precision cuts. Ensure the tool is centered with the workpiece. Use a ruler to check the alignment. The cutting edge must be at the correct height. Too high or too low affects the cut quality. Position the tool close to the workpiece but not touching. Secure the tool holder tightly to avoid movement.
Fine-tuning involves small adjustments for accuracy. Adjust the cutting depth gradually. Check the workpiece after each cut. Use a dial indicator for precise measurements. Always make small changes to avoid mistakes. Keep the tool sharp for cleaner cuts. Regularly check and adjust the tool position as needed.

Credit: www.pinterest.com
Advanced Tooling Technologies
Coolant-through tools make metal cutting easier. They have special channels for coolant. This keeps the tool cooler. It also helps to remove chips from the cutting area. Using coolant-through tools can make the tool last longer. They also help to improve the finish on the metal. Workers can cut faster and more accurately with these tools.
Smart tooling solutions are changing the way we work. They use sensors to collect data. This data helps to monitor the cutting process. Workers can see if the tool is wearing out. Smart tools can also adjust cutting parameters automatically. This helps to improve efficiency and accuracy. These tools can save time and reduce waste.
Safety Considerations In Metal Turning
Proper safety measures are essential when operating metal turning lathe tools. Wear protective gear and maintain equipment regularly to prevent accidents.
Personal Protective Equipment (ppe)
Always wear safety goggles to protect your eyes. Gloves keep your hands safe from sharp edges. Use ear protection to block loud noises. Wear a face shield for extra face protection. Steel-toed boots keep your feet safe from heavy objects. A dust mask helps you breathe clean air. Aprons protect your clothes from sparks and debris.
Best Practices To Prevent Accidents
Keep your workspace clean and organized. Always double-check machine settings before starting. Never rush your tasks. Use guards and safety devices on your lathe. Keep hands away from moving parts. Stay focused and avoid distractions. Turn off the machine before making adjustments. Report any malfunctioning tools immediately.
Conclusion: Maximizing Precision In Metal Turning
Optimizing precision in metal turning hinges on using high-quality lathe tools. Precision tools ensure accurate cuts and enhance overall efficiency.
The Importance Of Proper Tool Selection
Choosing the right tool is very important. It affects the quality of the work. Using the wrong tool can damage the material. It can also make the job slower. Always check the tool’s material and design. Different tools are made for different tasks. Proper selection saves time and money. It also extends the tool’s life. Always follow the manufacturer’s guidelines. This ensures safety and precision.
The Future Of Lathe Tooling Technology
New technologies are improving lathe tools. Smart tools can now monitor their own wear. They adjust for better performance. 3D printing is creating custom tools faster. This reduces wait times and costs. Advanced materials make tools last longer. They also work better with tough metals. Automation is making metal turning easier. Robots can do repetitive tasks. This reduces human error. The future looks bright for lathe tooling.
Frequently Asked Questions
What Are The Common Metal Lathe Tools?
Common metal lathe tools include turning tools, boring bars, parting tools, threading tools, and knurling tools.
Which Tool Is Used For Turning On A Lathe?
The tool used for turning on a lathe is the lathe cutting tool. It’s designed for precision cutting and shaping.
What Are The 5 Different Lathe Tools?
The five different lathe tools are the turning tool, facing tool, parting tool, grooving tool, and threading tool. These tools perform various operations like cutting, shaping, and threading on a lathe machine.
How Do I Choose A Turning Tool?
Choose a turning tool by considering material type, tool geometry, insert type, coating, and machine compatibility. Prioritize durability and performance.
Conclusion
Mastering metal turning lathe tools enhances your projects’ precision and quality. Choose the right tools for optimal results. Regular maintenance ensures longevity and peak performance. Invest time in learning techniques for improved craftsmanship. Your dedication to metalworking will yield impressive and professional outcomes.