Table of Contents
Metal turning finishes involve smoothing the surface of a metal part using various machining processes. These finishes enhance both appearance and functionality.
Metal turning is a fundamental process in manufacturing. It creates precise cylindrical parts by removing material from a workpiece. Various techniques, such as polishing, grinding, and buffing, achieve different finishes. These finishes range from rough to mirror-like, depending on the application.
Smooth finishes reduce friction and wear, extending the life of mechanical components. Accurate metal turning also ensures tight tolerances and optimal performance. Choosing the right finishing technique is crucial for achieving the desired quality and durability. This process is essential in industries like automotive, aerospace, and medical devices.
Introduction To Metal Turning Finishes
Surface finish is very important in metal turning. A smooth surface can improve part performance. It can also make the product look better. Quality surface finish can reduce wear and tear. It helps parts fit together properly. Poor surface finish can cause problems. It may lead to product failure. So, always aim for a good surface finish.
Metal turning is a machining process. It uses a cutting tool to remove material. The tool moves along the surface of the metal. This process creates a cylindrical shape. The workpiece rotates while the tool stays still. Speed and feed rate are important. They affect the finish and accuracy. Cutting fluids can help. They reduce heat and improve finish. Always use the right tool for the job.
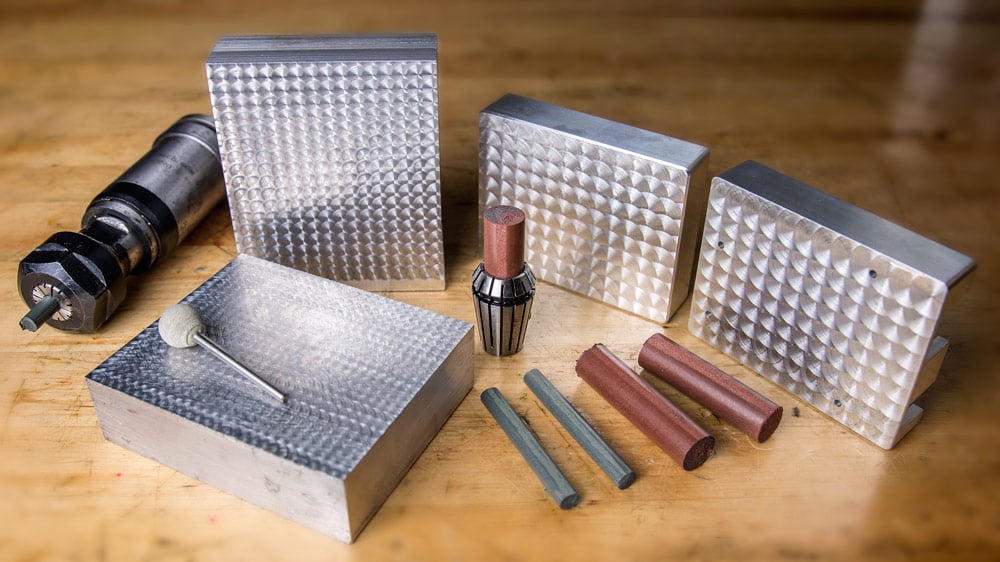
Credit: tormach.com
Types Of Metal Turning Finishes
Roughing cuts remove large amounts of metal quickly. These cuts are done to shape the metal roughly. Finishing cuts are used for precision. They create a smooth surface on the metal. Roughing cuts are faster but less accurate. Finishing cuts are slower but more precise. Both types of cuts are important in metalworking. A roughing cut starts the process. A finishing cut completes it. This ensures the final product looks good and fits well.
There are many popular metal turning finishes. Polished finishes are shiny and smooth. Satin finishes are less shiny but still smooth. Brushed finishes have fine lines on the surface. Matte finishes are dull and non-reflective. Each finish type has its own uses. Polished finishes are common in decorative items. Brushed finishes are used in tools and machinery. Matte finishes are used in cases where glare is a problem. Choosing the right finish is important for both function and appearance.
Material Considerations
Metal types affect the finish. Softer metals like aluminum have smooth finishes. Harder metals like steel need more work. Brass and copper are easier to shape. Titanium needs special tools.
Metal properties change the finish. Density affects the smoothness. Hardness impacts the shine. Some metals corrode easily. Rust can ruin the finish. Heat can change the metal. This affects the final look.
Credit: www.cybertruckownersclub.com
Tools For Optimal Turning
Pick the right cutting tool for the best metal finish. The tool must be sharp. A dull tool makes rough surfaces. The tool material matters too. Harder tools last longer. They make smoother cuts. Carbide tools are very popular. They stay sharp for a long time. High-speed steel tools are also good. They are less expensive.
Tool geometry affects the surface finish. The angle of the tool tip is crucial. A smaller angle gives a finer finish. Rake angle is also important. Positive rake angles reduce cutting forces. This results in smoother surfaces. Clearance angle prevents rubbing against the workpiece. Proper angles make a big difference.
Machine Settings And Techniques
Speed is the rate at which the machine’s spindle turns. It is crucial for metal turning. The right speed depends on the material. Too fast can cause overheating. Too slow can result in rough finishes.
Feed is the rate at which the cutting tool moves along the material. It affects surface finish. High feed rates can lead to roughness. Low feed rates can produce smoother surfaces.
Depth of cut is how deep the cutting tool penetrates the material. Larger depths remove more material. Smaller depths provide finer finishes. Balancing these three settings is key.
Interrupted cuts involve cutting materials with gaps or holes. They require careful settings. Choose the right speed and feed.
High-speed turning uses faster spindle speeds. It can improve surface finish. It also reduces machining time. Proper cooling is essential.
Threading involves cutting helical grooves. It requires precision. Use a sharp tool. Ensure correct feed and speed.
Surface Finish Measurement
To measure surface finish, different tools are used. Some common tools include profilometers and micrometers. These tools help in checking the smoothness of metal surfaces. Units like micrometers (μm) and nanometers (nm) are often used. A profilometer can scan the surface and provide details. It shows peaks and valleys on the surface. Micrometers measure the depth of these features.
Surface finish parameters tell us about the texture. Important parameters include Ra, Rz, and Rt. Ra is the average roughness. It shows the average height of peaks and valleys. Rz measures the difference between the highest peak and the lowest valley. Rt is the total height of the roughness profile. These parameters help in understanding the quality of the surface.
Troubleshooting Common Issues
Surface imperfections can be tiny scratches or rough patches. These issues affect the final look of the metal. Burrs are small, unwanted pieces of metal. They often appear on edges. Chatter marks look like small waves on the surface. They can be caused by tool vibration. Tearing appears as jagged lines. It often happens when the tool is too dull.
To prevent surface imperfections, use sharp tools. This helps in creating a smooth finish. Adjusting the speed of the machine can also help. Slow speeds reduce chatter marks. Use coolant to keep the tool and metal cool. This reduces the chances of tearing. For correcting existing issues, use fine sandpaper to smooth out burrs. Polishing compounds can help remove small scratches. Always inspect tools regularly to ensure they are in good condition.
Finishing Touches
Achieving smooth and precise metal turning finishes enhances both the appearance and functionality of machined parts. Expert techniques ensure high-quality surface textures and durability in metal components.
Secondary Finishing Processes
Secondary finishing processes improve metal surfaces. These processes add beauty and function. Common methods include polishing, buffing, and grinding. Polishing makes metal shiny. Buffing removes fine scratches. Grinding smooths rough edges. Each method serves a special purpose.
Achieving Aesthetic And Functional Surfaces
Good finishes improve the look and use of metal parts. Smooth surfaces prevent wear and tear. Shiny finishes catch the eye. Functional surfaces work better in machines. Finishing helps in many ways. Both looks and performance matter.
Case Studies And Applications
Explore the effectiveness of metal turning finishes through real-world case studies and practical applications. These insights reveal optimal techniques for achieving superior surface quality and precision in various industries.
Real-world Examples
Many industries need high-quality metal finishes. One example is the aerospace industry. They need precise parts for their airplanes. Another example is the automotive industry. They use metal turning for engine parts.
The medical field also benefits. They need smooth surfaces for surgical tools. Jewelry makers use metal turning too. They create beautiful, shiny pieces. These examples show how important metal turning is.
Industry-specific Requirements
Each industry has different needs. The aerospace industry requires very tight tolerances. Their parts must fit perfectly. The automotive industry needs durable and strong parts. These parts must withstand high stress.
The medical field needs hygienic and smooth surfaces. This ensures safety in surgeries. Jewelry makers need aesthetically pleasing finishes. Their pieces must look attractive. Meeting these needs requires special skills and tools.
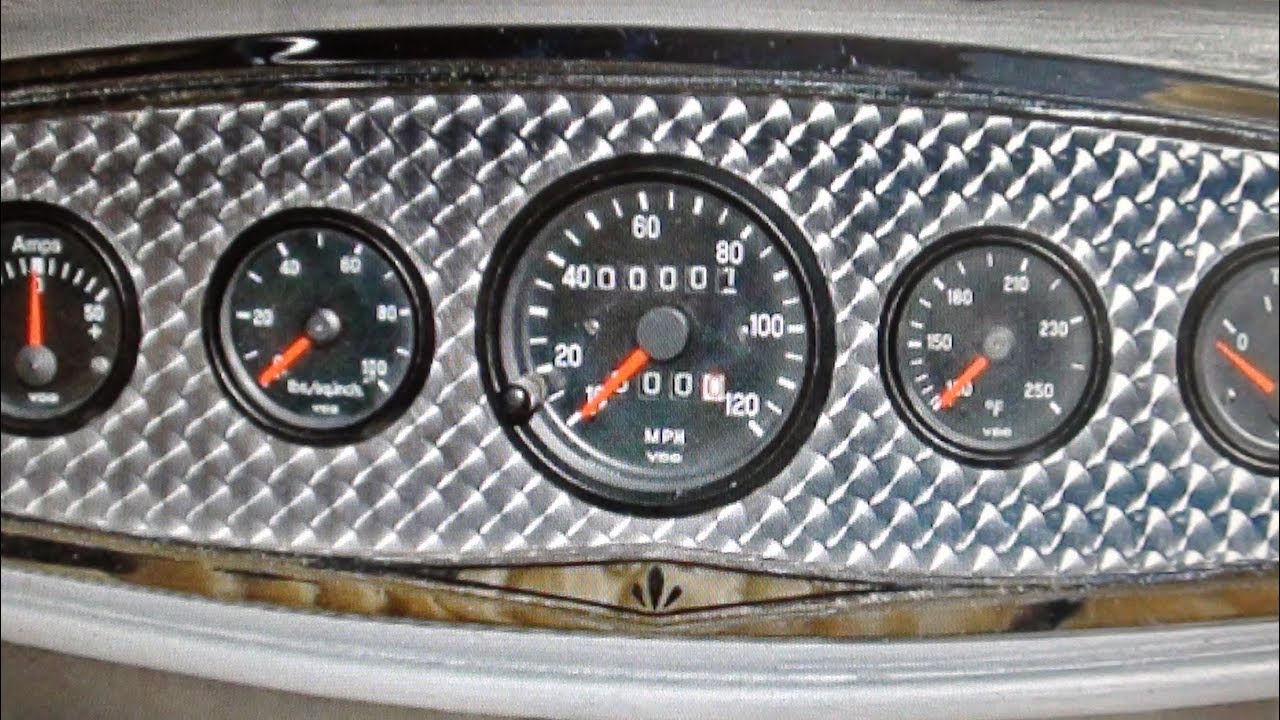
Credit: m.youtube.com
Future Trends In Metal Finishing
New machines are making metal finishing faster and more accurate. Robots help in the process and reduce errors. 3D printing is becoming more popular. This helps in making complex shapes easily. Laser technology is also helping in metal finishing. It gives a smooth and clean surface. Sensors are used to check the quality of the finish.
Eco-friendly methods are being used more often. Green chemicals are replacing harmful ones. This helps in keeping the environment clean. Water recycling systems are used to save water. Energy-efficient machines are reducing power usage. This makes the process more sustainable. Waste management is also being improved. This helps in reducing pollution.
Frequently Asked Questions
What Are The Different Types Of Metal Finishing Processes?
Types of metal finishing processes include electroplating, anodizing, powder coating, polishing, and galvanizing. These methods improve appearance, durability, and corrosion resistance.
What Are The Different Metal Finishes?
Different metal finishes include brushed, polished, satin, matte, anodized, electroplated, powder-coated, and galvanized. Each offers unique aesthetics and protection.
What Is The Best Finish For Metal?
The best finish for metal depends on its use. Popular options include powder coating, anodizing, and galvanizing. Powder coating offers durability and color variety. Anodizing enhances corrosion resistance and aesthetic appeal. Galvanizing provides strong rust protection. Choose based on the metal’s application and environmental conditions.
What Are The Three Finishes That Can Be Applied To Metal?
The three finishes for metal are painting, powder coating, and plating. These enhance durability, appearance, and corrosion resistance.
Conclusion
Achieving the perfect metal turning finish is crucial for quality and durability. Attention to detail ensures superior results. With the right techniques and tools, your projects will stand out. Keep experimenting to find what works best for you. Mastering these finishes will elevate your craftsmanship and impress clients.