Table of Contents
Metal turning a plate involves shaping a metal plate using a lathe. This process ensures precision and desired dimensions.
Metal turning is a fundamental machining process. It involves the use of a lathe to shape and size metal plates accurately. This technique is vital in various industries, from automotive to aerospace, due to its ability to produce precise and consistent results.
The lathe rotates the metal plate while a cutting tool shapes it, ensuring exact specifications. This process can handle different metals, including aluminum, steel, and titanium. Metal turning is essential for creating components that require tight tolerances and smooth finishes. Its versatility and precision make it a critical skill for machinists and engineers alike, contributing to the production of high-quality metal parts.

Credit: www.amazon.com
Introduction To Metal Turning
Metal turning is a method to shape metal. It uses a lathe. The lathe spins the metal. A cutting tool shapes the metal. This process can make cylinders, cones, and many other shapes. Metal turning is important for many industries. It helps make car parts, tools, and machines.
Essential Tools For Metal Turning
Several tools are needed for metal turning. The lathe machine is the main tool. It spins the metal. A cutting tool shapes the metal. Chucks hold the metal in place. Calipers measure the work. Files smooth the edges. These tools are essential for good metal turning.
Safety Precautions
Safety is very important in metal turning. Always wear safety glasses. They protect your eyes. Use gloves to protect your hands. Keep your work area clean. A messy area can be dangerous. Never wear loose clothing. It can get caught in the machine. Always follow safety rules. They keep you safe.
Preparing The Metal Plate
Choose a metal plate that fits your project. Aluminum and steel are popular choices. Ensure the material is free of defects.
Use a saw to cut the plate to the desired size. Wear safety gear like gloves and goggles. Measure twice, cut once to avoid mistakes.
Clean the plate with a degreaser to remove oils. Sand the surface to make it smooth. This helps in achieving a better finish.
Setting Up The Lathe
Secure the plate to the lathe chuck. Ensure it is tightly fixed. Use the provided wrench to tighten the bolts. Safety is important. Double-check the mounting before starting.
Select the appropriate speed for the material. Use the lathe’s manual for guidance. Adjust the speed dial to the correct setting. Start with a low speed. Increase gradually if needed. Keep the speed constant for a smooth finish.
Choose the right tool for the job. Use a cutting tool with a sharp edge. Insert the tool into the tool holder. Tighten the tool holder securely. Position the tool at the correct angle. Test the setup on a scrap piece first.
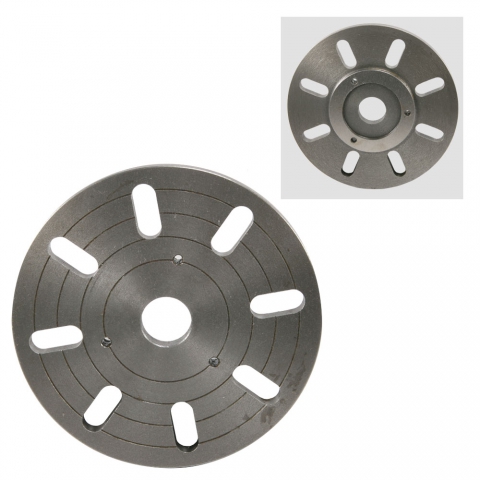
Credit: littlemachineshop.com
Mastering The Cutting Techniques
Rough cutting removes a lot of material quickly. Use a coarse tool for this step. This makes the plate easier to shape later. Be careful and always wear safety gear.
Fine cutting is for more precise work. Use a fine tool to get a smooth finish. It takes more time but is worth it. Always check your measurements.
Contouring gives the plate its final shape. Use different tools for curves and edges. Shaping needs patience and skill. Always work slowly and check your progress often.
Coolant And Lubrication
Efficient coolant and lubrication are essential for smooth metal turning of a plate. These elements reduce friction, prevent overheating, and enhance tool lifespan.
Types Of Coolants
Water-based coolants are very popular. They help keep the metal cool. Oil-based coolants give better lubrication. They are good for slower operations. Synthetic coolants are man-made. They combine the best features of both types. Semi-synthetic coolants are also available. They are a mix of water and oil-based coolants.
Application Techniques
Flood cooling is a common technique. It uses a lot of coolant. Mist cooling uses a fine spray. It saves on coolant but can be messy. High-pressure cooling is great for tough jobs. It pushes coolant into tight spaces. Through-tool cooling delivers coolant through the tool itself. This method is very efficient.
Precision Measurement Tools
Calipers are used to measure the distance between two sides of an object. They are very accurate. Micrometers are another tool for measuring small distances. They can measure even smaller distances than calipers. Both tools are essential for precision work.
Dial indicators help measure small changes in distance. They have a dial face that shows the measurement. The dial face is easy to read. These tools are used in many types of work. They help ensure everything is perfectly aligned.
Troubleshooting Common Issues
Vibrations can ruin your work. Use a steady hand and apply even pressure. Ensure your machine is well-maintained and tightly secured. Balancing the plate correctly helps reduce vibrations. Choose the right speed for your tool and material. Experiment with different settings to find the best balance.
Always check your tools for wear. Dull tools cause poor results. Replace worn tools quickly. Use the right tool for the job. Keep your tools clean and sharp. Proper maintenance extends tool life. Lubricate moving parts to prevent wear. Follow manufacturer guidelines for best practices.
A smooth surface finish is important. Clean the plate before starting. Use fine-grit sandpaper for a polished look. Make slow, steady passes with the tool. Keep the tool sharp and well-maintained. Adjust speed settings to avoid rough spots. Practice makes perfect for a smooth finish.
Finishing Touches
Sanding makes the metal surface smooth. Use fine-grit sandpaper for the best results. Always sand in one direction. This avoids scratches. After sanding, the next step is polishing. Polishing adds a shiny finish. Use a soft cloth and metal polish. Rub gently in circles. Repeat until the plate shines.
Inspect the plate after polishing. Look for any flaws or scratches. Check the plate’s shape and size. Use a ruler or measuring tape. Make sure the plate meets the required standards. If any flaws are found, fix them immediately. Quality control ensures a perfect final product.
Advanced Techniques
CNC machines help in turning metal plates with high precision. These machines use computer control to shape metals. The process reduces errors and increases efficiency. Complex designs are easily achieved with CNC.
Custom tools are made for specific metal turning tasks. These tools ensure better performance and accuracy. Unique shapes and sizes are possible with custom tooling. Special materials are used for these tools to increase durability.
Decorative turning adds aesthetic value to metal plates. Patterns and designs are created on the surface. Special tools and techniques are used for this process. Artistic skills are important for decorative turning.
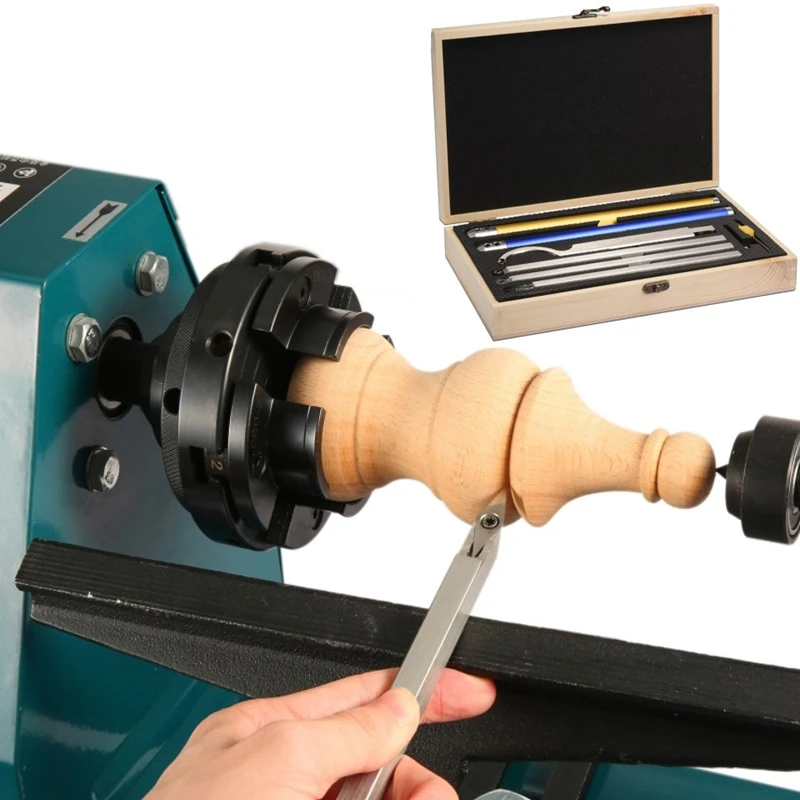
Credit: s.click.aliexpress.com
The Art Of Metal Turning
Metal turning has been around for centuries. Ancient civilizations used it to create tools and art. Craftsmen in ancient Egypt and Greece were skilled in this craft. They used simple tools to shape metal into beautiful forms. Metal turning was a respected skill. It required precision and patience.
Today, metal turning is still important. Factories use advanced machines for this process. These machines can produce parts for cars, planes, and even space rockets. Skilled workers operate these machines. They ensure each part meets exact specifications. Metal turning helps in creating durable and precise components.
Frequently Asked Questions
Is There A Difference Between A Wood Lathe And A Metal Lathe?
Yes, there is a difference. Wood lathes are designed for softer materials and higher speeds. Metal lathes handle harder materials and require more precision.
Can A Metal Lathe Be Used For Woodturning?
Yes, a metal lathe can be used for woodturning. You need to use appropriate cutting tools and adjust the speed.
What Tools Are Used To Spin Metal?
Metal spinning tools include lathes, mandrels, rollers, and trimming tools. Operators also use spinning chucks and lubricants.
How Do You Spin Metal?
Metal spinning involves rotating a metal disc on a lathe while applying pressure with a tool to shape it.
Conclusion
Mastering metal turning a plate enhances both skill and craftsmanship. Precision and patience are key to achieving excellence. Embrace this rewarding process and elevate your metalworking projects. Remember, practice makes perfect, and each effort brings you closer to mastery. Happy turning!