Table of Contents
Metal lathe turning tools are essential for shaping materials on a lathe. They cut, shape, and finish various metals.
Metal lathe turning tools play a vital role in machining. These tools are designed for precision cutting, shaping, and finishing of metal objects. They come in various types, including carbide-tipped, high-speed steel, and diamond-tipped tools, each suited for specific tasks.
Proper selection of lathe tools enhances efficiency and accuracy in metalworking projects. Investing in quality tools ensures longevity and better performance. Regular maintenance, such as sharpening and cleaning, is crucial for optimal results. Metal lathe turning tools are indispensable for hobbyists and professionals in the metalworking industry. These tools contribute significantly to creating intricate and detailed metal components.
Introduction To Metal Lathe Turning Tools
Turning tools are essential in metalworking. They shape and cut metal parts. These tools are used on a metal lathe. The lathe spins the metal, while the tool cuts. This process creates precise shapes and sizes. Skilled workers use these tools to make everything from bolts to car parts.
Turning tools have a big role in metalworking. They help in making accurate cuts. This is important for creating complex metal parts. The right tool makes the job easier and faster. It also ensures a smooth finish on the metal. Using the correct tool is crucial for safety.
Lathe tools have evolved a lot. Early tools were simple and manual. Modern tools are more advanced. They use special materials and designs. This makes them more efficient. Technology has improved the precision of these tools. Today’s tools can handle tougher materials. They also last longer.
Types Of Metal Lathe Turning Tools
High-Speed Steel (HSS) tools are very strong. They can cut through hard metals. They stay sharp for a long time. HSS tools resist wear and tear. They are cost-effective and easy to sharpen. HSS tools are versatile and reliable.
Carbide-tipped tools are extremely durable. They can cut at higher speeds. These tools last longer than HSS tools. Carbide-tipped tools produce a smoother finish. They are more resistant to heat. These tools are ideal for heavy-duty tasks.
Specialized tools have specific uses. They are made for unique tasks. Some are for cutting grooves. Others are for creating threads. Specialized tools increase efficiency. They improve the quality of the work. Choosing the right tool is crucial.
Tool Geometry And Material Selection
A cutting tool has several parts. The shank is the main body. The flank helps with cutting. The rake face removes metal. The cutting edge does the actual cutting. The nose is the tip of the tool. Each part is important for precision and efficiency.
Tool material impacts performance. High-speed steel is common and cheap. Carbide is harder and lasts longer. Ceramics resist heat but are brittle. Diamond tools are the hardest but expensive. Choose based on material and budget. Different jobs need different tools.

Credit: www.youtube.com
Toolholding And Workpiece Stability
Toolholders are very important. They keep tools steady. A steady tool gives accurate cuts. Use the right toolholder for each tool. This stops vibrations. Vibrations can ruin a piece. Always tighten the tool properly. Loose tools can be dangerous. Use collets or chucks. They hold tools better. Check toolholders often. Replace worn-out ones quickly.
Workpiece rigidity is key to good results. Secure the workpiece well. Use clamps or vises. Make sure it does not move. Moving workpieces cause mistakes. Check the setup before starting. Use steady rests for long pieces. They give extra support. Use tailstocks for extra stability. This helps when turning long items. Always double-check the setup. A stable workpiece gives better quality.
The Art Of Tool Sharpening
Using the right sharpening techniques is crucial for metal lathe turning tools. Always keep the tool at the correct angle. Use a whetstone or a grinding wheel. Do not press too hard. Light pressure works best for a sharp edge. Rotate the tool while sharpening. This ensures even wear. Cool the tool frequently to avoid overheating.
Regular maintenance keeps the tool edge sharp. Clean the tool after each use. Remove any metal shavings. Check the edge for nicks or dull spots. Sharpen the tool as soon as it shows signs of wear. A dull tool can ruin your workpiece. Store tools properly. Use protective covers to prevent damage.
Setting Cutting Parameters For Turning
Speed is how fast the workpiece spins. It is measured in RPM. Feed is the distance the tool moves per revolution. It is measured in inches per revolution. Depth of cut is how deep the tool cuts into the material. It is measured in inches.
To get a good surface finish, use a low feed rate. A smaller depth of cut helps too. Increase speed for a smoother finish. For high efficiency, use a larger depth of cut. A higher feed rate removes more material quickly. Balance these settings for the best results. Always use the right tool for the job.
Common Turning Operations
Facing makes the surface smooth and flat. It removes material from the end of the workpiece. Turning to diameter reduces the size of the workpiece. A lathe tool cuts along the length of the material. This process creates a uniform diameter.
Drilling creates holes in the workpiece. A drill bit is attached to the lathe. It moves into the material to make a hole. Boring enlarges existing holes. This process uses a single-point tool. The tool removes material from inside the hole, making it bigger.
Threading creates screw threads on the workpiece. A special tool cuts the threads. Grooving cuts narrow channels on the surface. These channels can be internal or external. Both operations require precise tools and careful control.
Troubleshooting Turning Challenges
Vibration and chatter can cause problems. Tighten all bolts and nuts to reduce vibration. Ensure the tool is sharp and correctly positioned. Use a steady rest to support long workpieces. Lower the cutting speed to minimize chatter. Balance the workpiece properly. Lubricate the tool and workpiece frequently.
Tool wear and breakage can slow down work. Use high-quality tools to reduce wear. Ensure the cutting edge is sharp. Adjust the cutting speed and feed rate properly. Lubricate the cutting area to prevent overheating. Check for tool alignment issues. Replace worn-out tools promptly to avoid breakage.
Advancements In Lathe Tool Technology
New coatings make lathe tools last longer. These coatings reduce wear and tear. Titanium nitride is a popular coating. It makes tools harder and more durable. Ceramic coatings are also used. They can handle high temperatures. This means tools stay sharp longer. Diamond coatings are the best. They are perfect for cutting very hard materials.
CNC lathes use computers to control the machine. This makes them very precise. They can make the same cut many times. This is good for mass production. Automation helps reduce mistakes. It also saves time. Machines can run without human help. This makes work faster and more efficient.

Credit: www.pinterest.com
Safety First: Best Practices In Lathe Operations
Always wear safety goggles to protect your eyes. Use ear protection to save your ears from loud noises. Gloves can protect your hands but must be tight-fitting. A face shield adds extra protection. Sturdy footwear keeps your feet safe. Wear a long-sleeve shirt to cover your arms.
Check your lathe for loose parts every day. Lubricate moving parts to keep them smooth. Clean debris off the machine after each use. Inspect electrical cords for damage. Replace worn-out tools and parts immediately. Keep a maintenance log for regular checks.
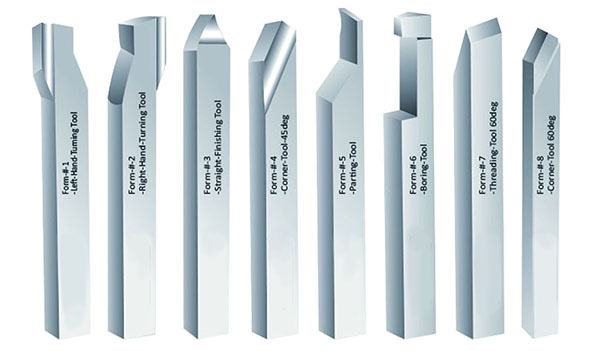
Credit: www.penntoolco.com
Frequently Asked Questions
What Are The Common Metal Lathe Tools?
Common metal lathe tools include turning tools, boring bars, parting tools, threading tools, and knurling tools. These tools shape, cut, and finish metal workpieces. Each tool serves a specific function in metalworking projects.
What Are The 5 Different Lathe Tools?
The 5 different lathe tools are:1. Turning tool. 2. Facing tool. 3. Boring tool. 4. Parting tool. 5. Threading tool.
Which Tool Is Used For Turning On A Lathe?
A lathe uses a cutting tool called a turning tool for shaping materials. It’s essential for precision machining.
What Tooling Do I Need For A Lathe?
You need a chuck, cutting tools, tool post, live center, tailstock, calipers, and a micrometer for a lathe.
Conclusion
Mastering metal lathe turning tools can elevate your projects. Choose the right tools for precision and efficiency. Practice regularly to enhance your skills. Investing in quality tools pays off in the long run. Stay updated with the latest advancements in lathe technology.
Happy turning!