Table of Contents
Metal for turning bowls usually involves materials like aluminum, brass, and steel. These metals offer durability and a smooth finish.
Metal turning for bowls is an art that requires precision and the right choice of materials. Aluminum is lightweight and easy to machine, making it popular for beginners. Brass provides a beautiful finish and is often used for decorative bowls.
Steel is strong and durable, ideal for bowls that need to withstand heavy use. Each metal has unique properties that affect the final product’s look and functionality. Choosing the right metal is crucial for achieving the desired results. Investing in quality materials ensures a superior finish and longer-lasting bowls, enhancing both the crafting experience and the final product.
The Art Of Turning Bowls
Turning bowls is an old art. People have been making bowls for centuries. Craftsmen use wood and metal tools. The process has changed over time. Early tools were simple. Modern tools are more advanced. This art has roots in many cultures. Each culture has its own style.
Today’s bowl turning uses both traditional techniques and modern technology. Many turners use electric lathes. These machines make the work easier. Some still prefer hand tools. The choice of material is also important. Wood and metal are common choices. Each material has unique properties. The final product can be very different. Some artists combine both materials. This creates unique and beautiful bowls.
Choosing The Right Metal
Durability is key for metals used in bowl turning. Metals should not break easily. They must be easy to shape. This helps in making smooth bowls. Heat resistance is another important property. Metals should not melt or warp. Strength and hardness are also vital. They ensure the bowl lasts long.
Metal | Properties |
---|---|
Aluminum | Lightweight, easy to shape, good heat resistance |
Brass | Strong, corrosion-resistant, aesthetically pleasing |
Stainless Steel | Very durable, rust-resistant, hard to shape |
Tools Of The Trade
Every metalworker needs a lathe. It is the most important machine. Cutting tools are also essential. These tools shape the metal. Measuring tools help ensure accuracy. A caliper is a good example. Lubricants are also needed. They keep the tools cool. This prevents damage to the metal and tools.
Safety gear is crucial for metalworking. Always wear safety goggles. They protect your eyes from flying metal. Gloves keep your hands safe from sharp edges. A face shield offers extra protection. Ear protection is also important. The machines can be very loud. Aprons protect your clothing and skin. Always work in a well-ventilated area.
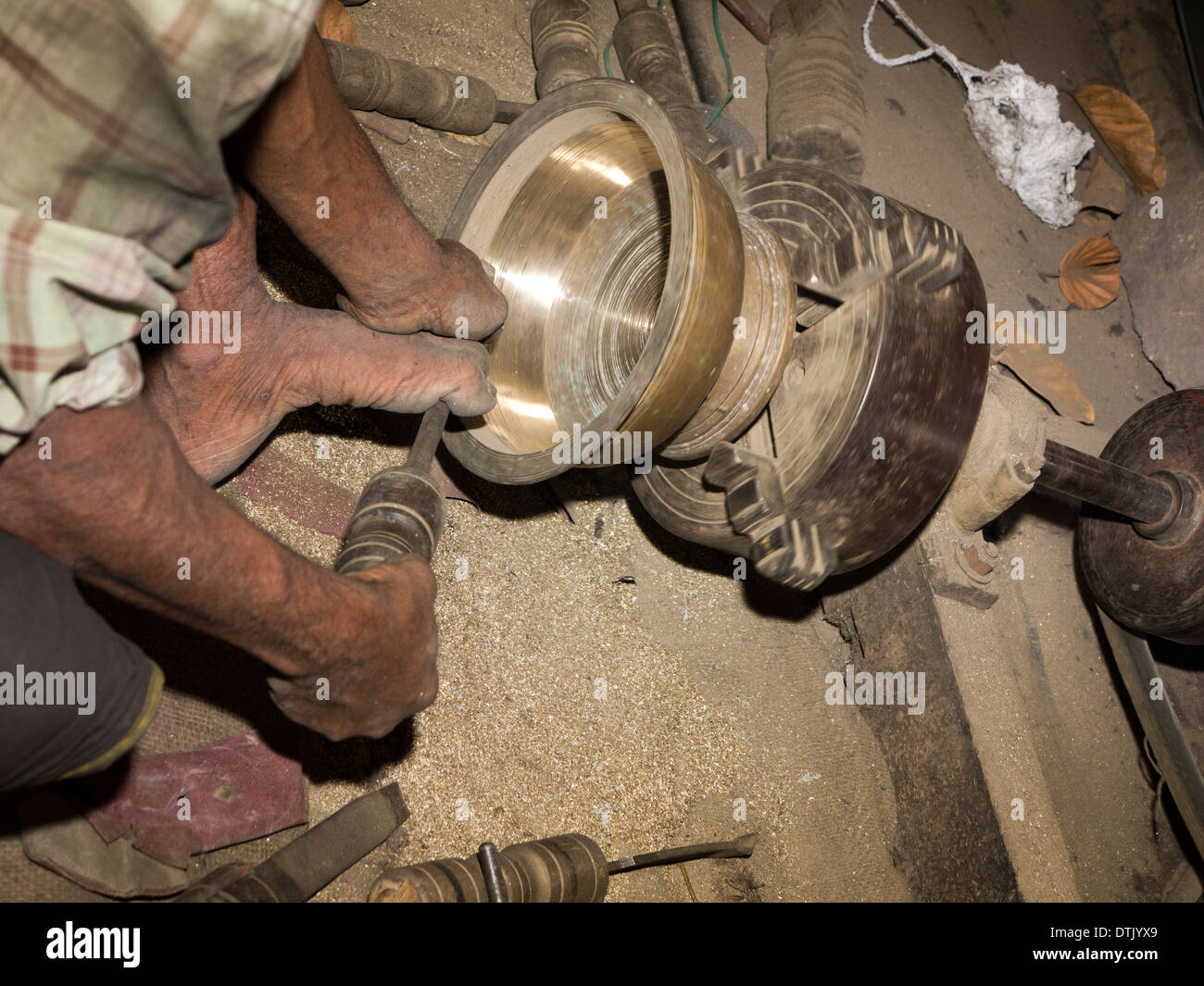
Credit: www.alamy.com
Preparing The Metal
First, measure the metal piece. Use a ruler or a measuring tape. Mark the measurements clearly. Next, use a metal saw. Cut the metal along the marked lines. Ensure the cuts are straight and clean. Use safety gear such as gloves and goggles. This protects you from metal shards. After cutting, inspect the edges. Remove any rough edges with a file.
Start by cleaning the metal. Use a cloth to remove dirt and dust. For stubborn grime, use a degreaser. Once clean, check for rust. Use sandpaper to remove any rust spots. Sand the entire surface lightly. This helps in removing minor imperfections. After sanding, wipe the surface again. Ensure it is smooth and ready for turning.
Techniques For Shaping
Start with a metal blank. Secure it on a lathe. Use a roughing gouge for shaping. Make slow and steady cuts. Keep the tool sharp. Aim for smooth, even surfaces. Check progress regularly. Adjust your technique as needed. Safety gear is important. Wear goggles and gloves.
Refine the shape with a skew chisel. Create intricate designs. Use a parting tool for grooves. Experiment with different angles. Try hollowing for deeper bowls. Apply varying pressure for texture. Polish the bowl for a shiny finish. Practice makes perfect. Always stay patient. Learn from each attempt.
Finishing Touches
Start with coarse sandpaper to remove rough edges. Move to finer grits for a smooth surface. Always sand in the same direction. Use a soft cloth to remove dust between grits. Polishing brings out the shine. Use a metal polish for the best results. Apply the polish with a clean cloth. Buff the surface until it shines.
Choose a finish that suits your metal type. Oil-based finishes work well on many metals. Apply a thin layer with a brush. Let it dry completely before adding more layers. Wax finishes are also popular. Apply wax with a soft cloth. Buff it to a shine for a smooth finish. Sealing the metal can protect it from rust. Use a clear sealant for a lasting finish.
Creative Design Ideas
Using patterns in metal bowls can make them unique. Try adding geometric shapes or floral designs. These designs can be etched or engraved. Patterns can also be stamped onto the metal. This makes the bowl more visually appealing. Patterns can be simple or complex. Choose a pattern that fits your style.
Mixing different metals can create a stunning effect. Combine copper, bronze, and brass for a rich look. Silver and gold can add a touch of luxury. You can also mix metal with other materials. Try wood or ceramic for a unique design. This adds contrast and texture to the bowl. Mixing materials can make each bowl one-of-a-kind.

Credit: m.youtube.com
Maintenance And Care
Always use warm water and mild soap. This helps to keep the metal shiny. Avoid harsh chemicals. They can damage the metal surface. Dry the bowls with a soft cloth. Make sure no water spots are left.
Never put metal bowls in the dishwasher. It can cause scratches. Clean them by hand for the best results. This way, your bowls will last longer.
Store metal bowls in a dry place. Moisture can cause rust. Use a protective cloth to wrap them. This will keep dust away. Check bowls regularly for signs of wear.
Polish the bowls with a metal polish. This keeps them looking new. Avoid stacking metal bowls. It can cause scratches. Place a cloth between each bowl if you need to stack them.
Showcasing Your Work
Craft intricate, durable bowls by mastering metal turning techniques. Showcase your artistry and elevate your metalworking skills with precision and creativity.
Display Options
Choose a good place to show your bowls. Use shelves to display them. Put lights to make them shine. Clear cases can protect bowls from dust. Arrange bowls by size or color. This makes them look nice. Use stands to hold the bowls. This shows their shapes well. Rotate the display often to keep it fresh. Add tags with details about each bowl. This helps people learn more.
Selling And Marketing
Tell friends about your bowls. Use social media to reach more people. Post pictures and videos of your work. Show the process of making bowls. This makes it interesting. Join craft fairs and art shows. This helps you meet buyers. Make a website to sell online. Write clear descriptions of each bowl. Set fair prices. Offer discounts to first-time buyers. Build a mailing list to keep in touch with customers.

Credit: www.amazon.com
Frequently Asked Questions
What Is The Best Tool For Bowl Turning?
The best tool for bowl turning is a wood lathe. It allows precise shaping and smoothing of wooden bowls.
What Do I Need For Bowl Turning?
You need a lathe, turning tools, bowl blanks, a face shield, and sandpaper for bowl turning. Safety equipment is essential.
What Is The Best Steel For Woodturning Tools?
High-speed steel (HSS) is the best for woodturning tools. It offers durability, sharpness, and heat resistance.
What Size Lathe For Bowl Turning?
A lathe with a 12-inch swing and 16-inch bed length is ideal for bowl turning. This size accommodates most projects.
Conclusion
Choosing the right metal for turning bowls ensures quality and durability. Stainless steel and aluminum are top choices. They offer precision and longevity. Always consider the specific needs of your project. With the right metal, your turning bowls will stand out.
Happy crafting and enjoy the process!