Table of Contents
Lathe metal turning tools shape and finish metal workpieces with precision. They are essential in machining processes.
Lathe metal turning tools are vital for the manufacturing industry. These tools enable the precise cutting, shaping, and finishing of metal workpieces, ensuring high-quality outcomes. They are designed to work with a lathe, a machine that rotates the workpiece on its axis to perform various operations.
Different types of lathe tools, such as cutting, facing, and threading tools, are used for specific tasks. The right selection of tools enhances productivity and accuracy, making them indispensable in metalworking. For machinists and hobbyists alike, understanding and using lathe metal turning tools is crucial for achieving desired results in metal fabrication projects.

Credit: www.pinterest.com
Introduction To Lathe Metal Turning
Lathe metal turning tools shape and refine workpieces with precision. Essential for machining, they ensure accurate cuts and smooth finishes.
Brief History Of Metal Turning
Metal turning is an ancient skill. People used simple tools to shape metal. Early lathes were powered by hands and feet. In the 18th century, machines became more advanced. The Industrial Revolution brought new innovations. Metal turning tools improved over time.
Basic Principles Of A Lathe
A lathe rotates the metal workpiece. Tools shape the metal as it spins. The operator controls speed and movement. Different tools create different shapes. Safety is very important in metal turning. Proper training is necessary for using a lathe.
Types Of Lathe Metal Turning Tools
Cutting tools are very important in metal turning. They cut and shape metal. High-speed steel tools are common. They stay sharp for a long time. Carbide tools are also used. They are very hard and can cut tough metals. Diamond tools are the hardest. They give a very smooth finish. Each tool has a special job. Some tools cut straight. Others make curves or grooves. Using the right tool makes the job easier.
Advanced projects need specialized tools. Boring bars make holes inside metal pieces. Parting tools cut off parts of the metal. Threading tools make screw threads. Knurling tools create textured surfaces. Each tool helps make special designs. They are used by skilled workers. These tools make very detailed parts.
Setting Up For Success
Choose the right tool for the job. Hard metals need carbide tools. Softer metals work well with high-speed steel tools. Use parting tools for cutting off sections. Boring bars make holes larger. Facing tools smooth out surfaces. Always pick the correct size for your tool.
Clean the lathe machine first. Remove any debris or old material. Check for any damage. Tighten all bolts and screws. Ensure the chuck is secure. Set the speed according to the material. Use the right lubricant for the job. Always wear safety gear.
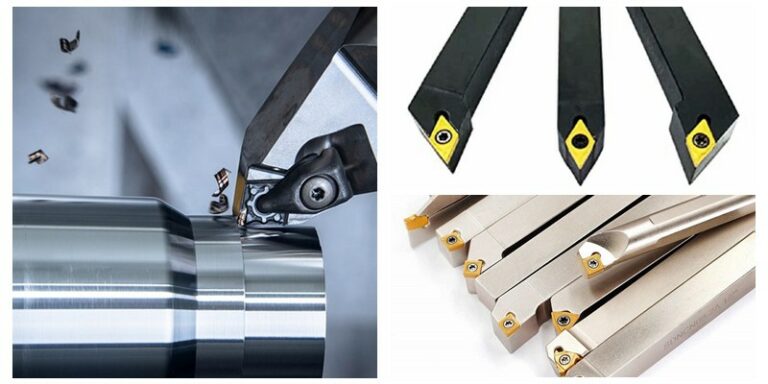
Credit: waykenrm.com
Fundamental Metal Turning Techniques
Lathe metal turning tools shape materials with precision, utilizing various cutting techniques for efficient metalworking. These tools include carbide, high-speed steel, and diamond-tipped options.
Facing Operations
Facing makes the end of a metal workpiece flat. It uses a lathe tool to cut across the end. The tool moves perpendicularly to the workpiece’s axis. This process ensures a smooth, flat surface. Precision is crucial for good results. Always use the right speed and feed rate.
Turning Operations
Turning reduces the diameter of a workpiece. It uses a cutting tool to remove material. The workpiece spins while the tool moves parallel to its axis. This creates a cylindrical shape. Turning can make parts of different sizes. Speed and feed rate adjustments give better control. Quality tools are essential for accurate turning.
Advanced Turning Techniques
Thread cutting involves precise movements. A lathe machine helps in this process. The lathe cuts threads on the metal surface. Use the correct tool for the best results. Set the lathe speed carefully. Always measure the thread depth. Double-check the pitch of the thread. Regularly lubricate the tool and workpiece. This ensures smooth cuts and extends tool life. Always follow safety rules.
Taper turning creates angled surfaces on metal. There are various methods to do this. Form tool method uses a tool shaped like the taper. The tool is fixed, and the workpiece turns. Compound rest method involves setting the lathe’s compound rest at an angle. The workpiece is turned while the tool moves along the taper. Tailstock set-over method shifts the tailstock to create the taper. Each method has its own advantages. Choose the right method for your project.
Tool Maintenance And Care
Always clean your tools after use. Use a soft cloth to wipe off metal shavings. Apply a light coat of machine oil to prevent rust. Store tools in a dry place. Use a toolbox or a tool rack. Label your tools for easy access. Keep sharp objects covered. Check for damage before storing. Regular maintenance extends tool life.
Use a grinding wheel to sharpen. Hold the tool steady while grinding. Keep the angle consistent. Dip the tool in water to cool it. Repeat until the edge is sharp. A whetstone can also be used. Always lubricate the stone. Sharpen in one direction only. Test the sharpness on scrap metal. Regular sharpening ensures precision.
Safety Measures In Metal Turning
Proper use of lathe metal turning tools ensures operator safety and precision in machining tasks. Wearing protective gear and following guidelines prevents accidents and enhances efficiency.
Personal Protective Equipment
Always wear safety glasses to protect your eyes. Gloves can shield your hands from sharp edges. Ear protection helps guard against loud noises. Face shields offer extra protection from flying debris. Steel-toed boots can protect your feet. Aprons and long sleeves can protect your skin. Respirators can help you avoid inhaling harmful dust and fumes.
Safe Operation Practices
Inspect your tools before use. Ensure the work area is clean and organized. Secure the workpiece tightly to avoid movement. Always use guards and shields. Turn off the lathe before making adjustments. Keep hands away from moving parts. Do not wear loose clothing or jewelry. Follow the manufacturer’s instructions for each tool.
Troubleshooting Common Issues
A poor finish on your workpiece can be frustrating. Start by checking the sharpness of your tool. A dull tool often causes rough surfaces. Make sure to use the correct cutting speed for the material. High speeds can create unwanted marks. Low speeds might not cut cleanly. Also, ensure your tool is aligned properly. Misalignment leads to uneven cuts.
Tool chatter can ruin your work. Reduce chatter by tightening the tool post. A loose tool post vibrates more. Slow down the feed rate to minimize vibrations. Using a shorter tool can also help. Longer tools are less stable. Finally, check that your workpiece is secured firmly. A shaky workpiece causes chatter.
Enhancing Precision And Accuracy
Precise measurements are crucial in metal turning. Use a caliper to measure the workpiece. Ensure the caliper is clean. Zero the caliper before use. Use a micrometer for more accuracy. Calibrate tools regularly for the best results.
Consistent cuts require proper technique. Use a sharp tool for smooth cuts. Adjust the cutting speed based on the material. Feed rate must be steady. Align the tool with the workpiece. Ensure even pressure during the cut. Practice makes perfect.
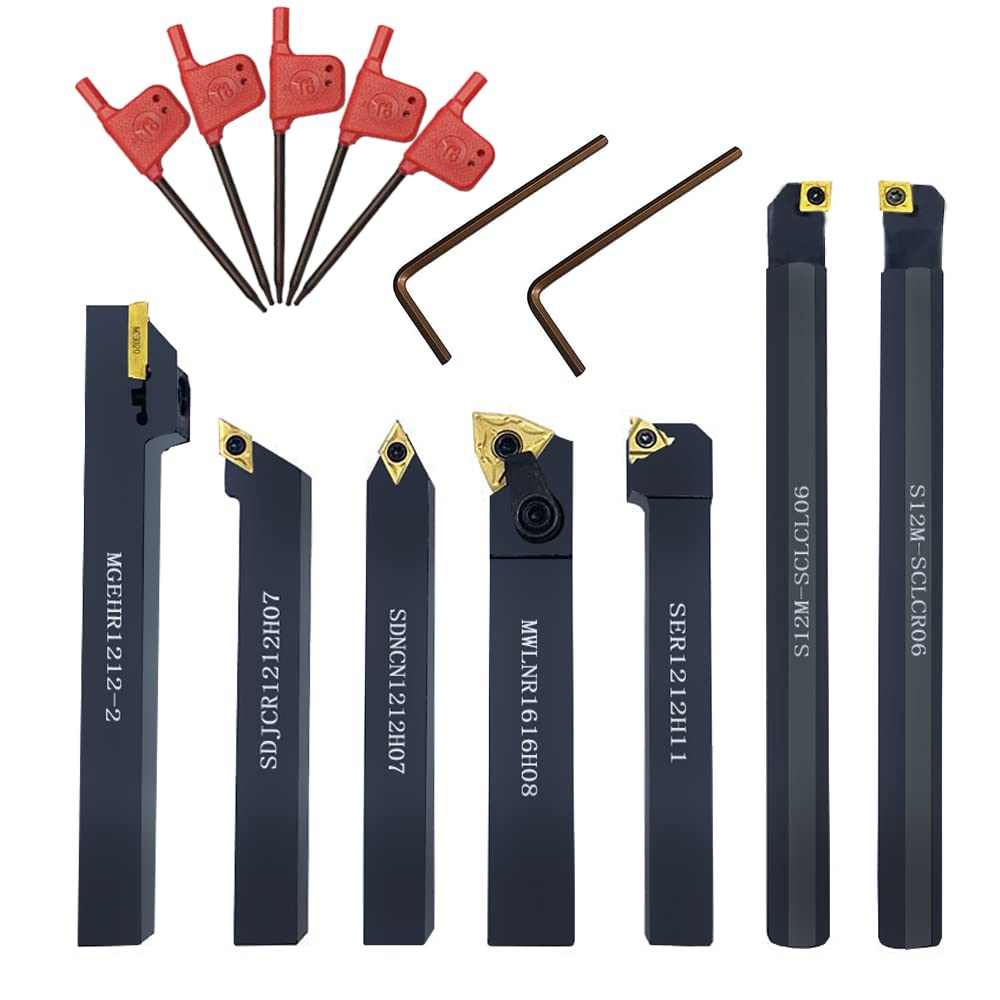
Credit: bigeasymart.com
Projects To Master Your Skills
Start with a basic cylinder. This project helps you learn basic cutting. Create a simple ring next. This project teaches you how to cut inside a shape. Practice threading with a basic nut and bolt. This helps you learn precision cutting. Finally, make a basic handle. You will learn how to shape and polish metal.
Create a complex gear. This project will test your accuracy and patience. Make a detailed figurine. This will push your shaping skills to the limit. Try making a working engine part. You need to measure and cut with great precision. Lastly, build a multi-part assembly. This will test your assembly skills.
Tips From The Experts
Always use sharp tools. Sharp tools cut better and faster. Clean your tools after each use. Dirty tools do not work well. Measure your materials twice. This helps avoid mistakes. Wear safety gear. Safety is very important. Organize your workspace. A clean space helps you work better. Follow the instructions. Instructions help you understand what to do.
Plan your work before you start. Planning helps you stay on track. Use the right tool for each job. The right tool makes the job easier. Take breaks when needed. Rest helps you stay focused. Ask for help if you need it. Experts can give good advice. Practice makes perfect. The more you practice, the better you get. Stay patient and never rush. Rushing can cause mistakes.
The Future Of Metal Turning
New technologies are changing metal turning. Computer Numerical Control (CNC) machines make cutting more precise. These machines can work faster. They also reduce human error. Automation is increasing in factories. This makes production quicker and more efficient. 3D printing is also being used. It helps in making complex parts easily.
Many eco-friendly practices are now popular. Companies are using recycled materials. They aim to reduce waste. Smart machines are another trend. These machines can learn from data. They improve with time. Customization is also on the rise. Customers want unique parts. Factories are now able to meet these demands.
Frequently Asked Questions
What Are The Types Of Lathe Metal Turning Tools?
Lathe metal turning tools include roughing tools, finishing tools, parting tools, and threading tools. Each serves a specific purpose in metalworking.
How To Choose The Right Lathe Tool?
Choose based on material, desired finish, and the specific task. Consider factors like tool shape and cutting speed.
What Is The Purpose Of A Roughing Tool?
A roughing tool removes large amounts of material quickly. It’s ideal for initial shaping before fine finishing.
Why Use High-speed Steel (hss) Tools?
HSS tools are durable and can withstand high temperatures. They are versatile and provide a good finish.
Conclusion
Mastering lathe metal turning tools enhances precision and efficiency in metalworking projects. These tools are essential for any machinist. Invest in quality tools and practice regularly to achieve the best results. Stay updated with the latest advancements in lathe technology to maintain a competitive edge.
Happy turning!