Table of Contents
Grinding turning tools involves sharpening the edges and shaping them for precise cutting. It ensures tools remain efficient and accurate.
Properly grinding turning tools is essential for achieving optimal performance in machining tasks. Sharp tools reduce wear and tear on machinery, leading to longer tool life and better-quality workpieces. The process involves using a grinding wheel to hone the cutting edges of the tool, ensuring they are sharp and properly angled.
Attention to detail during grinding can improve cutting efficiency and accuracy. Always use the appropriate grinding wheel for the material of the tool. Regular maintenance and sharpening can save time and costs in the long run by minimizing tool replacement and enhancing productivity.
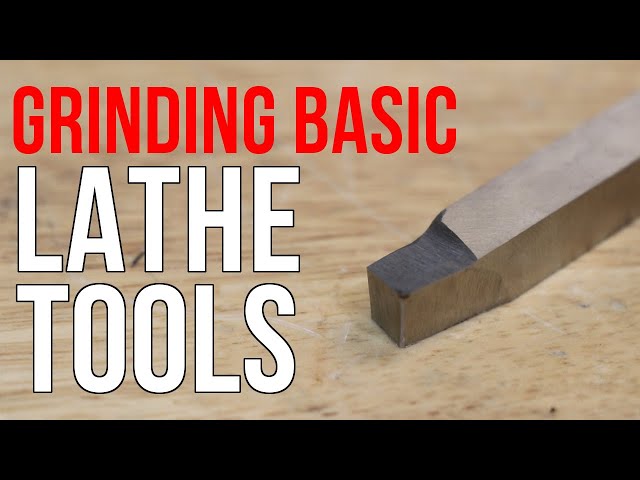
Credit: m.youtube.com
The Art Of Grinding Turning Tools
Sharpening turning tools needs care and skill. Begin by understanding the correct angles. Use a consistent approach to maintain these angles. Avoid overheating the tool. It can damage the metal. Always keep the tool cool and lubricated. Use short, controlled passes with the grinder. This prevents uneven edges. Regularly check the sharpness of the tool. A sharp tool makes cleaner cuts. Practice these principles to master tool sharpening.
Having the right tools is important. Use a bench grinder with a stable base. A grinding wheel with the correct grit is essential. Tool rests help maintain angles. A coolant system prevents overheating. Safety gear like goggles and gloves are crucial. Sharpening jigs can assist in precision. Quality equipment ensures better results.
Types Of Turning Tools And Their Uses
High-speed steel tools are affordable and easy to sharpen. They can cut most materials. Carbide-tipped tools stay sharp longer. They work well on tough materials. Ceramic tools handle high speeds. They resist heat very well. Diamond tools are the hardest. They give the best finish but are costly.
Consider the material you are cutting. Use carbide for hard materials. Think about the speed of your machine. Ceramic tools work best at high speeds. Check the cost of tools. High-speed steel is cheaper. Look at the finish you need. Diamond tools give the best finish.
Setting Up Your Grinding Station
Pick a spot with good lighting. Ensure the area has enough space for all your tools. Make sure the surface is stable and won’t shake. Keep the area free of clutter. Proper ventilation is key to remove dust. Avoid placing your station near flammable materials. Ensure there are power outlets nearby for your tools.
Keep your grinding wheels on a dedicated rack. Use labeled boxes for small parts like screws and bolts. Arrange wrenches and other tools on a tool board. Place a fire extinguisher within reach. Store safety gear like goggles and gloves in a drawer. Ensure everything is easy to access and use. A clean station improves efficiency and safety.
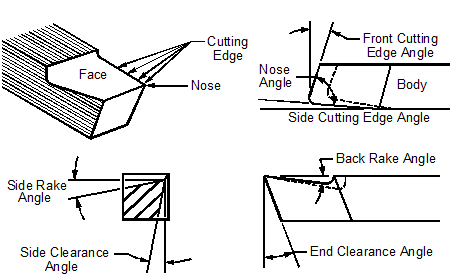
Credit: www.metalartspress.com
Safety First: Pre-grinding Precautions
Wearing protective gear is very important. Use safety glasses to protect your eyes. Always wear gloves to protect your hands. Face shields can protect your face from sparks. Ear protection can save your hearing from loud noises. Make sure your work area is clean and free from clutter.
Grinding can be dangerous if not done properly. Sparks can cause fires. Small particles can get in your eyes and cause injuries. Machines can be very loud, which can hurt your ears. Always stay alert while grinding. Follow all safety rules to stay safe.
Step-by-step Guide To Grinding
First, gather all your materials. You need a turning tool, a grinding wheel, and safety gear. Wear safety goggles to protect your eyes. Ensure the grinding wheel is clean and free from debris. Check that the tool rest is secure and in place. Use a marker to outline the areas you need to grind. This helps you stay accurate.
Start the grinding wheel and hold the tool firmly. Apply gentle pressure and move the tool slowly against the wheel. Keep your hands steady and use even motions. Cool the tool often to prevent overheating. A hot tool can lose its hardness and become useless. Check your progress frequently. You want a sharp edge, but not too thin.
Troubleshooting Common Grinding Issues
Overheating during grinding can damage tools. Use a coolant to keep the temperature down. Water-based coolants are very effective. Check the flow of coolant regularly. Ensure the grinding wheel is not too hard. A softer wheel may help. Also, reduce the speed of the grinder. Lower speeds generate less heat. Finally, take breaks to allow the tool to cool down.
Uneven edges can ruin a tool’s performance. First, check the alignment of the tool. Proper alignment is crucial. Use a jig to hold the tool steady. A steady tool is easier to grind evenly. Next, examine the grinding wheel. It should be free from wear and tear. A damaged wheel causes uneven grinding. Rotate the tool frequently during grinding. This will help achieve even edges. Lastly, inspect the edges after grinding. Make sure they are smooth and even.
Maintaining Your Grinding Wheels
Dressing your grinding wheel is very important. This keeps the wheel in good shape. A dressing tool is used for this job. It removes worn-out grains. The wheel surface becomes clean and sharp again. This process helps to avoid burning and chatter. Always dress the wheel before and after use.
Replace the grinding wheel if it has cracks. A cracked wheel is very dangerous. If the wheel is worn out, it needs replacement. A worn-out wheel cannot grind properly. It may damage the tool. Always check the wheel before use. Safety should always come first.
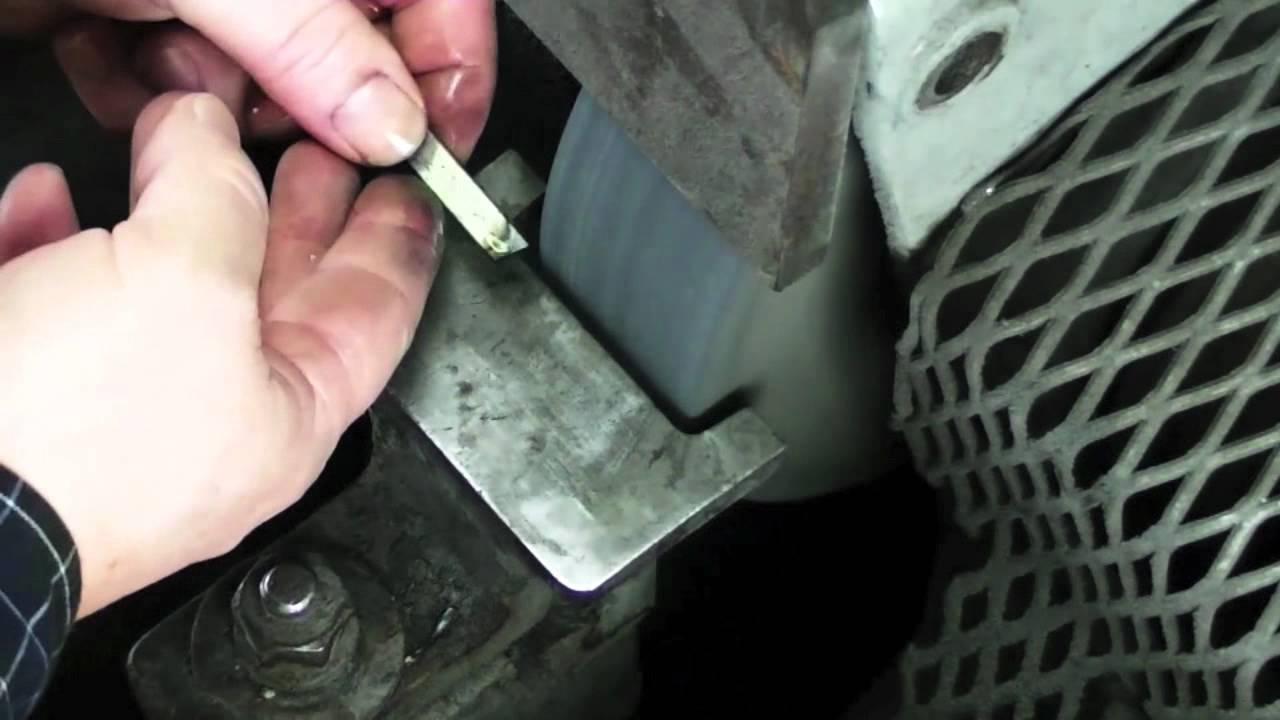
Credit: www.youtube.com
Advanced Grinding Techniques
Precision grinding is an essential skill for creating sharp turning tools. This technique ensures tools are effective and long-lasting. Sharp tools make cleaner cuts and improve productivity. Consistent practice helps to master this art. Focus on maintaining the correct angle and pressure. Use quality grinding wheels for the best results. Proper cooling prevents overheating and damage. Always wear safety gear to protect yourself.
Different tools require different grinding angles. High-speed steel tools often use a 60-degree angle. Carbide tools might need a steeper angle. Experiment to find what works best for your tools. Always check the manufacturer’s recommendations. Using the right angle increases tool life and performance. Practice makes it easier to achieve the perfect angle. Remember to inspect tools regularly for wear and tear.
From Grinding To Turning: Testing Your Tool
First, check the sharpness of your tool. Use a fingernail to test the edge. A sharp tool catches easily. Next, perform a cutting test on a piece of wood. Observe how smoothly it cuts. Sharp tools produce clean and smooth cuts. Also, listen for any odd sounds. Sounds can indicate issues with sharpness.
If your tool needs adjustments, use a honing stone. Gently rub the edge on the stone. Check the sharpness again. Repeat if necessary. Ensure the tool is evenly sharp along the edge. Finally, test the tool on wood again. Adjust as needed for perfect performance.
Frequently Asked Questions
How To Grind Your Own Lathe Tools?
To grind your own lathe tools, use a bench grinder. Shape the tool’s angles precisely. Keep the tool cool by dipping it in water frequently. Use fine grit for a smooth finish. Ensure proper angles for cutting efficiency. Always wear safety gear.
What Is The Best Grit For Sharpening Turning Tools?
The best grit for sharpening turning tools is typically 120 to 180 grit. This range offers a balance of sharpness and durability.
What Grinding Wheel To Sharpen Lathe Tools?
Use a white aluminum oxide grinding wheel to sharpen lathe tools. Choose a wheel with a grit of 60 or 80.
How To Grind Cutting Tools?
To grind cutting tools, use a bench grinder with the appropriate wheel. Hold the tool at the correct angle. Apply light pressure and move consistently. Frequently cool the tool in water to prevent overheating.
Conclusion
Mastering the art of grinding turning tools enhances precision and efficiency. Proper techniques extend tool life and improve outcomes. Consistent practice and patience yield the best results. Invest time in learning, and your machining projects will benefit greatly. Happy grinding!