Table of Contents
Chucks for metalturning lathes securely hold the workpiece during machining. They ensure precision and stability.
Metalturning lathes are essential in machining for shaping metal parts. The chuck, a critical component, grips the workpiece firmly, allowing for precise cuts and smooth finishes. Different types of chucks, such as three-jaw, four-jaw, and collet chucks, cater to various applications and workpiece shapes.
Three-jaw chucks are versatile and self-centering, ideal for round workpieces. Four-jaw chucks offer adjustable jaws for irregular shapes. Collet chucks provide high precision and grip for smaller, delicate tasks. Choosing the right chuck enhances efficiency and accuracy, ensuring quality results in metalturning projects. Proper maintenance of chucks extends their lifespan and ensures consistent performance.
Introduction To Metalturning Lathes
Metalturning lathes are vital in shaping metals. They help create precise components. These machines rotate the metal piece. A cutting tool shapes it. This allows for uniform and accurate results. Lathes are used in many industries. They are essential in manufacturing. They save time and effort. Metalturning lathes are versatile tools. Their importance cannot be overstated.
The Role Of Chucks In Metalworking
Chucks hold the metal piece in place. They are mounted on the lathe’s spindle. This ensures stability during machining. Chucks come in various types. Some common types are three-jaw and four-jaw chucks. Each type serves different purposes. Chucks enhance precision. They provide a firm grip. This reduces errors. Chucks are crucial for achieving accurate results. They are vital for safe and efficient metalworking.
Evolution Of Metalturning Lathes
Metalturning lathes have evolved over time. Early lathes were simple. They were operated manually. Modern lathes are more advanced. They feature computerized controls. This increases accuracy. It also speeds up the process. Modern lathes are more efficient. They can handle complex tasks. The evolution of lathes has revolutionized metalworking. It has made the process faster and more precise.

Credit: www.amazon.com
Types Of Chucks For Metalturning
Three-Jaw Universal Chucks are common in metalturning. They have three jaws that move together. This makes them great for holding round or hexagonal workpieces. Most people find them easy to use. They can center the workpiece quickly. These chucks are not good for irregular shapes.
Four-Jaw Independent Chucks offer flexibility. Each jaw moves separately. This allows for holding odd-shaped pieces. They are ideal for square or rectangular items. These chucks take more time to set up. They offer precise centering for complex shapes.
Collet Chucks provide high precision. They use a collet to hold the workpiece. This ensures firm and accurate gripping. These chucks are perfect for small, delicate pieces. They are often used in high-speed machining. Changing collets can be time-consuming.
Magnetic Chucks use magnetic force to hold the workpiece. They are ideal for flat, ferrous materials. These chucks allow for quick setup and removal. They are not suitable for non-magnetic materials. Magnetic strength can vary with material thickness.
Key Features Of Metalturning Chucks
Metalturning chucks use jaws to hold workpieces. These jaws come in different designs. Some have two jaws, others have three or more. Jaws are usually made of hardened steel for durability. Some chucks have replaceable jaws. This allows for flexibility in operations. Soft jaws can be customized for specific tasks. Hard jaws offer better grip and longer life.
Gripping force is key for secure holding. High gripping force ensures the workpiece stays in place. Accuracy is vital in metalturning. Chucks must hold the workpiece precisely. This ensures high-quality results. Runout is a common term for accuracy. Low runout means better precision. Always check the gripping force and accuracy ratings. This will help in choosing the right chuck.
Quick change chucks save time. They allow for fast jaw changes. This is useful in production settings. Quick change capabilities reduce downtime. Operators can switch jaws in minutes. This improves efficiency. Some chucks come with tool-less change features. These are even faster. Always look for chucks with quick change options. It makes your work easier and faster.
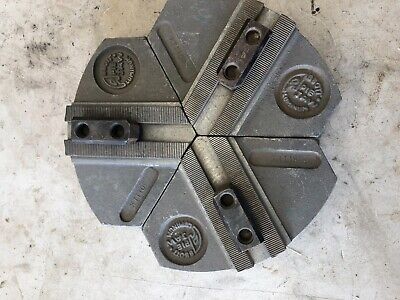
Credit: www.ebay.com
Enhancing Precision In Metalturning
Chuck accuracy is vital for metalturning. A precise chuck holds the workpiece firmly. This reduces wobble and ensures clean cuts. Accurate chucks lead to better finishes on your metal pieces. They also help in achieving tighter tolerances. Without a precise chuck, errors can occur. These errors can ruin your project. Always check the accuracy of your chuck before starting.
Runout is the wobble in the chuck. Adjusting for runout is crucial. Use a dial indicator to measure it. Make small adjustments to minimize runout. This ensures your workpiece spins true. Reducing runout improves the quality of cuts. It also extends the life of your tools. Always make sure to check for runout before each project.
Keeping your chuck aligned is important. Misalignment can cause inaccurate cuts. Regularly check the alignment of your chuck. Use alignment tools if needed. Proper alignment leads to better precision. It also reduces wear on your lathe. Always maintain your chuck for best results.
Grip Enhancement Techniques
Choose the right chuck jaws for your work. Soft jaws are great for delicate items. Hard jaws hold tough materials well. The size of the jaws should match the size of the workpiece. Always check the jaw compatibility before using.
Apply chuck grease to moving parts. This helps in smooth movement. Use lubricants to prevent rust. This ensures the chuck lasts longer. Always use the right type of lubricant for your chuck.
Clean the chuck after every use. Remove any debris or metal shavings. Inspect for wear and tear regularly. Tighten any loose parts. This maintains a strong grip on the workpiece. Regular maintenance ensures safety and efficiency.
Choosing The Right Chuck For Your Lathe
Understand the size and shape of your workpiece. Some chucks handle large pieces better. Others are good for small, delicate items. Consider the material of your workpiece. Metal, wood, and plastic have different needs. Choose a chuck that provides a secure grip.
Ensure the chuck matches your lathe’s spindle size. Check the mounting system. Not all chucks fit every lathe. Verify the weight capacity of your lathe. Heavy chucks may affect performance. Always read the manufacturer’s guidelines.
High-quality chucks are often expensive. Budget-friendly options exist, but may lack durability. Consider long-term use. Investing in a better chuck can save money over time. Look for warranties or return policies. These offer protection for your purchase.
Safety Practices In Metalturning
Always ensure the chuck is securely tightened before starting the lathe. Check for any loose parts or debris around the chuck area. Use the right tools to tighten the chuck properly. Avoid over-tightening to prevent damage. Regularly inspect the chuck for wear and tear.
Wear protective gloves to handle sharp metal edges. Keep your work area clean to avoid accidents. Use proper tools to lift and move metal pieces. Avoid using your bare hands to touch sharp surfaces. Always focus on your task to prevent injuries.
Know the location of the emergency stop button on your lathe. Practice using it regularly to ensure you can stop the machine quickly. Ensure the emergency stop button is always accessible. Inform others in the workshop about its location. Regularly check the functionality of the stop button.
Advanced Chuck Technologies
Hydraulic chucks use fluid power to grip the workpiece. This offers strong and reliable clamping. Pneumatic chucks use air pressure for gripping. They are faster and more efficient for quick changes. Both types are popular for their precision and ease of use. They help in reducing downtime and increasing productivity.
Programmable chucks can be controlled by a computer. This makes them ideal for automated systems. They allow for precise and repeatable operations. These chucks can easily adapt to different tasks. This reduces the need for manual adjustments. They are perfect for high-volume production environments.
Future chuck designs will focus on smart technology. This includes sensors for real-time monitoring. It also includes adaptive clamping mechanisms. These innovations will improve accuracy and efficiency. Lightweight materials will be used to reduce energy consumption. The goal is to make chucks more user-friendly and sustainable.
Maintenance And Troubleshooting
Regular cleaning is essential. Use a soft brush to remove debris. Always inspect for wear and tear. Check the jaws for alignment. Lubricate the moving parts lightly. Make sure to avoid over-lubrication. Keep the chuck free from rust. Store in a dry place when not in use.
If the chuck is not gripping, check for debris. Clean the jaws thoroughly. Misalignment can cause issues. Ensure the jaws are seated properly. Look for worn-out parts. Replace them if necessary. A noisy chuck may need lubrication. Apply oil sparingly to moving parts.
Seek professional help if issues persist. Complex repairs should be handled by experts. If the chuck shows extensive wear, consult a technician. Unusual noises may indicate serious problems. Never ignore consistent performance issues. Skilled technicians can provide accurate diagnosis and repair.
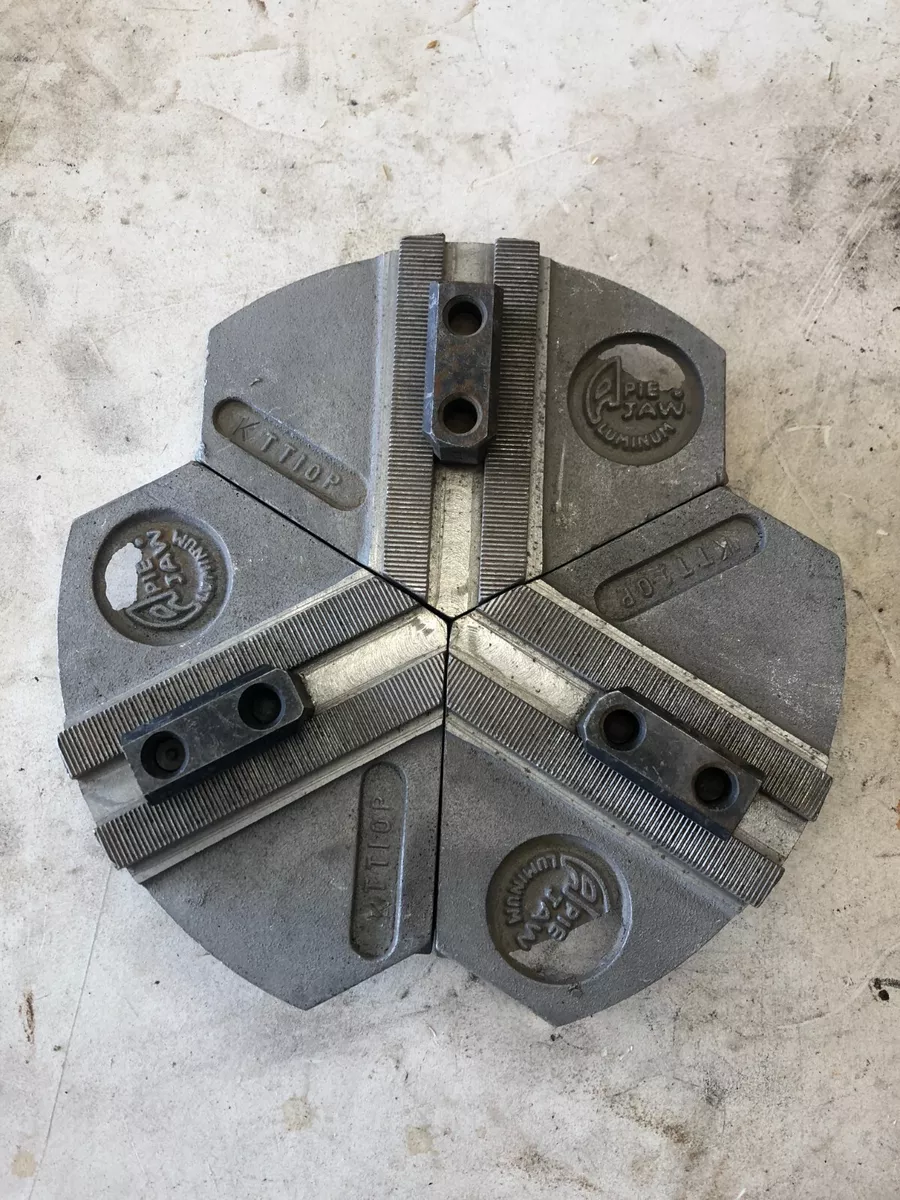
Credit: www.ebay.com
Frequently Asked Questions
What Are The Two Different Types Of Chucks Used On A Metal Lathe?
The two types of chucks used on a metal lathe are three-jaw chucks and four-jaw chucks. Three-jaw chucks are self-centering, while four-jaw chucks allow independent jaw movement for irregular shapes.
How Do I Know If A Chuck Will Fit My Lathe?
Measure your lathe’s spindle size and thread. Check the chuck’s compatibility with these specifications. Verify mounting type and backplate.
What Are The Two Most Common Types Of Chucks On A Lathe Turning Center?
The two most common types of chucks on a lathe turning center are three-jaw chucks and four-jaw chucks. Three-jaw chucks are best for round workpieces, while four-jaw chucks offer flexibility for irregular shapes. Both are essential for various machining tasks.
Are Lathe Chucks Universal?
Lathe chucks are not universal. Different lathes require specific chucks. Always check compatibility before purchasing.
Conclusion
Choosing the right chuck for your metalturning lathe enhances precision and efficiency. Quality chucks ensure smoother operations and better results. Invest in reliable brands to avoid frequent replacements. Proper maintenance extends the lifespan of your equipment. Upgrade your lathe with the best chucks to achieve exceptional metalturning performance.