Table of Contents
Turning tools for a lathe shape and cut materials like wood and metal. They ensure precision and efficiency in machining tasks.
Lathe turning tools are essential for shaping and cutting materials with high precision. These tools come in various types, each designed for specific functions such as roughing, finishing, threading, and parting. High-speed steel (HSS) and carbide are common materials used for these tools due to their durability and performance.
Proper selection and maintenance of turning tools enhance productivity and extend tool life. Operators must choose the right tool based on the material and desired outcome. Understanding the functionality and application of each type can significantly improve machining efficiency and quality.
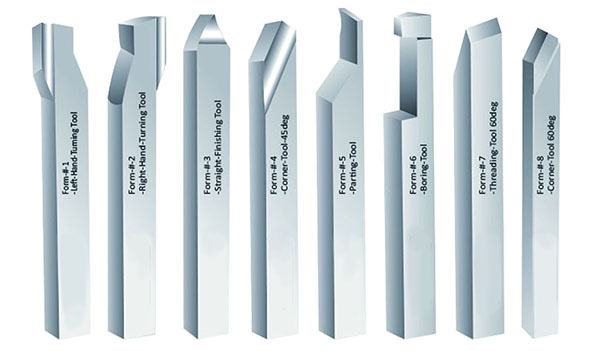
Credit: www.penntoolco.com
Introduction To Lathe Turning Tools
Lathe turning tools are crucial for shaping materials. They help in both woodworking and metalworking. These tools cut, shape, and finish materials. Woodworkers use them for making furniture and sculptures. Metalworkers use them for creating machine parts. Each tool has a specific purpose. Some tools are designed for rough cutting. Others are for fine detailing. This makes them very versatile.
There are many types of lathe turning tools. Each type serves a unique function. Chisels are common for wood. Boring bars are used for hollowing out materials. Parting tools help to cut off pieces. Facing tools make flat surfaces. Grooving tools create grooves in materials. This variety allows for many different projects. These tools can handle both simple and complex tasks.
Types Of Lathe Turning Tools
Lathe turning tools come in various types, including roughing tools, finishing tools, and parting tools. Each tool serves a specific purpose, ensuring precision and efficiency in machining tasks.
Cutting Tools: Material And Geometry
Lathe cutting tools come in many types. High-speed steel (HSS) is very common. Carbide tools are harder and last longer. Ceramic tools can handle high heat. Tool geometry also matters. Rake angle affects cutting efficiency. Clearance angle prevents tool rubbing. Nose radius impacts surface finish. Proper selection ensures good performance.
Specialized Tools For Advanced Techniques
Specialized tools help with complex tasks. Boring bars enlarge holes with precision. Threading tools create screw threads. Parting tools cut deep grooves. Knurling tools add textured patterns. Form tools shape profiles in one pass. Each tool serves a unique purpose. Choosing the right tool is key to success.
Selecting The Right Tool For The Job
Choosing the perfect turning tools for a lathe ensures precision and efficiency. Quality tools enhance performance, leading to superior craftsmanship.
Considering Material And Shape
Material of the workpiece is vital. Hard materials need tough tools. Soft materials need sharp tools. Shape of the tool affects the cut. Round tools are good for smooth finishes. Square tools are good for rough cuts.
Tool Angles And Cutting Edge
Tool angles change the cut quality. Smaller angles make fine cuts. Larger angles make rough cuts. The cutting edge should be sharp. A dull edge can spoil the work. Choose angles based on the job type.
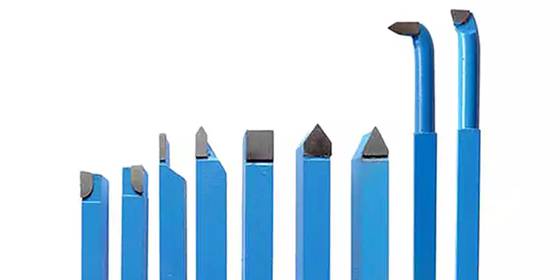
Credit: waykenrm.com
Maintaining Your Tools
Proper care of turning tools for lathe ensures precision and longevity. Regular cleaning and sharpening maintain optimal performance and safety.
Sharpening Best Practices
Sharpen your tools regularly. Use a grinding wheel to keep edges sharp. Cool the tool often to prevent overheating. Use safety gear like goggles and gloves. Check angles to ensure precision. Clean the tools after sharpening. This prevents rust and damage. Store tools properly to maintain sharpness.
Storage And Handling
Store tools in a dry place to avoid rust. Use protective cases to prevent damage. Label tools for easy identification. Keep tools organized in drawers or racks. Handle tools with care to extend their life. Inspect tools regularly for wear and tear. Replace damaged tools immediately for safety.
Advanced Tips For Improved Precision
Keep the tool rest close to the workpiece. This helps to reduce vibrations. Adjust the tool rest height so the tool is at center height. This ensures better cutting performance. Remember to move the tool rest as you progress. This keeps you cutting efficiently. Always secure the tool rest tightly. A loose tool rest can cause accidents.
Speed and feed rate are crucial for precision. Use a lower speed for harder materials. Soft materials can handle higher speeds. Adjust the feed rate to match the speed. A faster feed rate can lead to rough finishes. Slower feed rates give smoother surfaces. Always monitor the cutting process. This helps avoid mistakes and ensures safety.

Credit: www.amazon.com
Tool Upgrades And Accessories
Upgrading your lathe tools can improve your work. High-speed steel (HSS) tools are great for many tasks. Carbide-tipped tools last longer and cut harder materials. Quick-change tool posts save time during tool swaps. They make your work faster and smoother.
Digital readouts show accurate measurements. This helps you make precise cuts. Coolant systems keep your tools cool. This stops them from overheating. Lighting systems help you see your work better. Chip guards keep your workspace clean and safe.
Safety First: Best Practices
Ensure proper maintenance and handling of turning tools for lathe operations to maximize safety and efficiency. Always wear protective gear and follow manufacturer guidelines for optimal performance.
Personal Protective Equipment
Wear safety goggles to protect your eyes. Always use ear protection to avoid hearing damage. Put on a dust mask to keep dust out of your lungs. Choose tight clothing to prevent it from getting caught. Use sturdy gloves to protect your hands. Wear non-slip shoes for a firm grip. Always secure long hair under a cap.
Safe Handling And Operation
Inspect tools before use to ensure they are in good condition. Keep the work area clean to prevent accidents. Always turn off the lathe before making adjustments. Use both hands to control tools firmly. Never leave the lathe unattended while it’s running. Use appropriate speed settings for the material. Maintain a safe distance from moving parts.
Real-world Applications And Projects
Turning tools for lathe machines enable precision in crafting intricate components. Industries like automotive and aerospace rely on these tools for high-quality production. Efficient and versatile, they enhance productivity and accuracy in various real-world applications.
Case Studies
Turning tools help create many objects. Engineers use them to make car parts. Craftsmen use them to make wooden bowls. Jewelry makers use them to create unique rings. These tools are useful in many fields.
Students also use these tools in school projects. They learn about precision and craftsmanship. Professionals and hobbyists both find turning tools valuable. They help in creating detailed and accurate pieces.
Project Ideas To Test Your Skills
Try making a wooden pen. You can also create a metal chess piece. Another project is making custom handles for tools. These projects help in learning new techniques.
Beginners can start with simple shapes. Advanced users can try more complex designs. Each project helps improve your skills. You can also join a club to share ideas. Working with others can be very helpful.
Frequently Asked Questions
Which Tool Is Used For Turning On A Lathe?
A turning tool, often made of high-speed steel or carbide, is used for turning on a lathe.
What Are The 5 Different Lathe Tools?
The 5 different lathe tools are turning tools, facing tools, boring tools, parting tools, and threading tools. Each tool serves a specific function in metalworking and woodworking.
What Tooling Do I Need For A Lathe?
You need cutting tools, a chuck, a tailstock, a tool post, a live center, and a tool holder for a lathe.
How Do I Choose A Turning Tool?
Choose a turning tool by considering material, tool geometry, cutting speed, feed rate, and surface finish requirements. Select a tool compatible with your machine and workpiece material. Prioritize durability and performance to achieve precise results.
Conclusion
Mastering turning tools for lathe operations enhances precision and efficiency. Choose the right tool for optimal results. Regular maintenance ensures longevity. Invest time in learning techniques to improve your craftsmanship. Stay updated with the latest advancements. Elevate your projects with the right turning tools and see the difference in quality and performance.