Table of Contents
Segment Metal Turning is a machining process that removes material from a workpiece. It uses a cutting tool to achieve the desired shape.
Segment Metal Turning is essential in manufacturing industries for creating precise components. This technique involves rotating the workpiece while a cutting tool removes material to shape it accurately. The process ensures high precision and quality, making it ideal for producing parts used in various applications, from automotive to aerospace.
Skilled machinists operate lathes and other machinery to perform metal turning, ensuring that each piece meets exact specifications. This method enhances efficiency and reduces waste, making it a cost-effective solution in manufacturing. Understanding Segment Metal Turning helps in appreciating its critical role in producing durable and reliable metal components.
Introduction To Segment Metal Turning
Segment Metal Turning involves the precise cutting of metal parts using specialized machinery. This technique ensures high accuracy and efficiency in manufacturing. Ideal for creating complex shapes and detailed components.
The Significance Of Precision
Precision in metal turning is crucial. It ensures that parts fit together perfectly. This reduces waste and saves money. High precision leads to better product quality. It also improves safety in machinery. Precision can extend the life of the parts. Tools wear out less quickly. Precision is vital for efficiency and cost-effectiveness.
Evolution Of Metal Turning
Metal turning has evolved over the years. Early methods used simple tools. Modern techniques use advanced machinery. These machines are computer-controlled. They offer higher accuracy. Automation has also played a big role. It speeds up the process. Automation reduces human error. Metal turning continues to improve with technology.
Essential Equipment For Metal Turning
Lathes are machines that spin metal. There are different types of lathes. Engine lathes are common. They are good for many tasks. Turret lathes are used for mass production. CNC lathes are controlled by computers. They are very precise. Bench lathes are small and used for small jobs.
Cutting tools are important in metal turning. High-speed steel tools are strong and last long. Carbide tools are even stronger. They can cut hard metals. Ceramic tools are used for very hard materials. Cutting tools need to be sharp. They make smooth cuts. Lubricants help cool the metal. They also reduce friction.
Segmentation In Metal Turning
Segmentation helps in improving precision. It makes the cutting process faster and more efficient. This approach reduces waste and saves material. Tool wear is minimized, leading to longer tool life. It also enhances surface finish and product quality. Better control over the process is achieved. This results in higher productivity and lower costs. With segmentation, complex shapes can be easily created. This method is ideal for high-volume production.
A study on a large manufacturing firm showed increased efficiency. They implemented segmentation in their metal turning process. The results were impressive. Production rates increased by 25%. Tool life was extended by 40%. Surface finish quality improved significantly. Another case involved a small workshop. They saw a reduction in material waste by 15%. Customer satisfaction also went up due to better quality products. Both cases highlight the real-world advantages of segmentation.
Material Considerations
Material considerations in segment metal turning include selecting appropriate alloys and understanding their machinability to ensure precision and efficiency. Prioritizing factors like tool wear resistance and thermal conductivity can significantly impact the quality of the final product.
Choosing The Right Metal
Choosing the right metal is very important. Each metal has unique properties. These properties affect the turning process. Stainless steel is strong but hard to cut. Aluminum is easier to turn but not as strong. Brass is soft and easy to work with. Pick the metal that matches your needs.
Impact On Precision And Waste
Precision in metal turning is crucial. Hard metals can make precision difficult. Softer metals might bend or warp. Waste is another issue. Harder metals produce more waste. Softer metals waste less but may need more finishing. Choosing the right metal reduces waste and improves precision.
Process Optimization Techniques
Tool path strategies are very important. A smooth path reduces wear and tear. It also improves efficiency. Shorter paths save time. They also save energy. Each turn should be precise. Precision ensures quality. A good strategy also minimizes errors. Errors can be costly.
Speed and feed rate are key factors. Both affect the finish quality. High speed may cause tool wear. Low speed can waste time. The feed rate should match the material. Different materials need different rates. Adjustments should be made carefully. Incorrect settings can damage tools. They can also ruin the workpiece.
/smstreet/media/media_files/n248Lf0EXiOtJTvLTO9I.jpg)
Credit: smestreet.in
Quality Control Measures
Quality control is very important in metal turning. Inspection and testing ensure that every piece meets the required standards. During inspection, workers check each piece for defects. Testing involves using tools to measure dimensions and tolerances. Only pieces that pass these tests move forward. This process helps in maintaining high quality.
Tolerances are the allowed variations in measurements. Keeping tight tolerances ensures parts fit together perfectly. Workers use calipers and micrometers to check tolerances. Machines are calibrated regularly to keep accuracy. If a part does not meet the tolerance, it is reworked or discarded. This keeps the production line efficient and reliable.
Technological Advancements
CNC machines have transformed metal turning. They offer greater precision and efficiency. These machines can run 24/7 with minimal supervision. This means increased productivity for manufacturers. Automation also reduces human errors. This leads to better quality products. Robots can handle repetitive tasks. This frees up human workers for more complex jobs.
New cutting tools enhance metal turning. They last longer and cut faster. Some tools have special coatings. These coatings reduce wear and tear. Software advancements also play a role. They help in designing complex parts easily. Some software can even simulate the turning process. This helps in identifying any issues before actual production starts. The use of 3D printing for prototyping is also growing. It allows for quick and cost-effective testing of designs.
Challenges And Solutions
Complex parts are hard to handle. Accuracy is very important. Machines must be very precise. Operators need good training. Advanced tools help a lot. Proper planning is key. Mistakes can be costly. Using 3D models helps in planning. Quality checks are needed often.
Downtime is very bad for business. Regular maintenance reduces downtime. Quality tools last longer. Training operators well is important. Using good software helps. Sensors can warn of problems early. Automation can speed up work. Good planning saves money. Tracking performance helps find issues.
Future Of Precision Machining
Predictive maintenance helps machines work better. Sensors can find problems before they happen. This saves time and money. Machines last longer when cared for well. Less downtime means more work gets done. Factories can plan better with this system. Predictive maintenance makes work safer. Workers stay safe when machines run well.
Factories use adaptive manufacturing systems to make many items. These systems can change quickly. They can make small or big items. Computers help these systems work well. Adaptive manufacturing systems save materials. They help make many products fast. These systems can learn and get better over time. Workers need less training with these systems.

Credit: www.researchgate.net
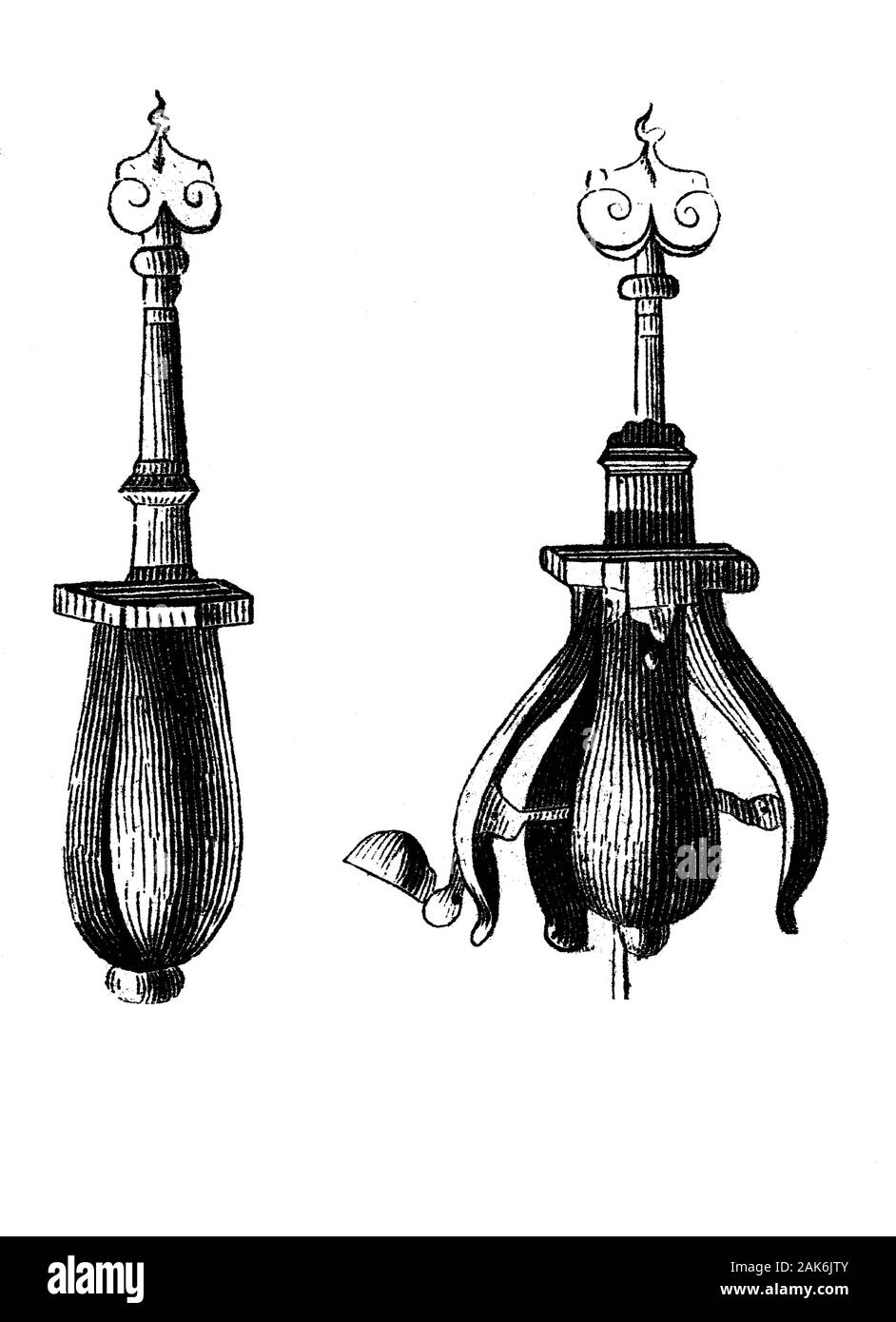
Credit: www.alamy.com
Frequently Asked Questions
What Is The Angle Of A Segmented Bowl?
The angle of a segmented bowl depends on the number of segments. For a 12-segment bowl, each angle is 30 degrees.
What Is The Difference Between Turning Between Centres And Face Plate Turning On A Wood Lathe?
Turning between centers supports wood at both ends, ideal for symmetrical shapes. Faceplate turning secures wood at one end, perfect for bowls.
What Is Segment Metal Turning?
Segment metal turning involves shaping metal into segments using a lathe. It is a precise machining process. This technique is essential in manufacturing and engineering industries.
How Does Segment Metal Turning Work?
Segment metal turning uses a lathe to rotate metal. A cutting tool shapes the metal into segments. This process ensures precision and accuracy.
Conclusion
Mastering segment metal turning can significantly enhance efficiency and precision in manufacturing processes. By implementing the best practices discussed, businesses can achieve superior results and reduce production time. Stay updated with the latest techniques to maintain a competitive edge. Embrace these methods to ensure quality and consistency in your metal turning projects.