Table of Contents
Turning tools for a lathe are essential for shaping materials. They come in various types, including carbide, steel, and diamond-tipped.
Turning tools are crucial for any lathe operation. They determine the precision and finish of the final product. Carbide-tipped tools are popular for their durability and cutting efficiency. High-speed steel tools offer versatility and are excellent for general-purpose use. Diamond-tipped tools provide superior cutting for hard materials.
Choosing the right tool depends on the material and the desired finish. Proper maintenance and sharpening extend the life of turning tools. Investing in high-quality turning tools enhances productivity and ensures better outcomes. Always prioritize safety and proper handling during lathe operations.

Credit: www.amazon.com
Introduction To Lathe Turning Tools
Turning tools are essential for shaping materials on a lathe. These tools can cut, drill, knurl, or sand materials. Lathe turning tools come in various shapes and sizes. Each tool serves a specific purpose in metalworking.
Turning tools are crucial in metalworking for shaping metal parts. These tools help achieve precise dimensions and smooth finishes. They are used to create components for machines, engines, and other devices. Different tools are required for different tasks. Each tool is designed for a specific operation, such as cutting or drilling. Using the right tool ensures accuracy and efficiency.
Lathe Type | Recommended Tools |
---|---|
Engine Lathe | High-speed steel tools, carbide tools |
Turret Lathe | Indexable tools, form tools |
Toolroom Lathe | Precision tools, boring bars |
Automatic Lathe | Carbide inserts, threading tools |
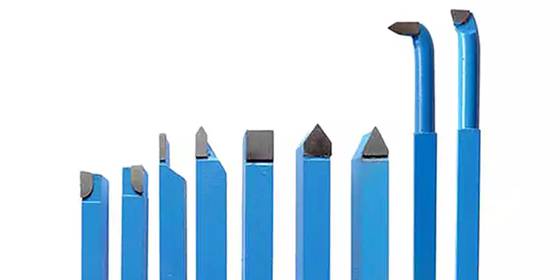
Credit: waykenrm.com
Materials And Properties Of Turning Tools
Turning tools for lathe machines are crafted from high-speed steel, carbide, and ceramic materials. These tools offer excellent durability, heat resistance, and precision for efficient metalworking.
Common Materials Used In Tool Manufacturing
Turning tools are made from high-speed steel (HSS). They are also made from carbide and ceramic. HSS tools are less costly and easy to shape. Carbide tools are harder and stay sharp longer. Ceramic tools are very hard and resist heat well.
Heat Resistance And Durability Concerns
Tools must resist high heat during cutting. HSS tools can handle moderate heat. Carbide tools can handle higher heat. Ceramic tools can handle the highest heat. Durability is also vital. Durable tools last longer and save money. Carbide and ceramic tools are more durable than HSS tools.
Categories Of Lathe Turning Tools
Cutting tools are essential for shaping materials. Inserts are small cutting pieces that fit into holders. Holders keep the inserts in place for precise cuts. Many inserts are made of carbide or ceramic. These materials are very strong and durable. Holders come in different shapes to fit various needs. Using the right combination of inserts and holders ensures smooth and accurate cuts.
Boring tools make holes larger. They are useful for refining holes. Threading tools create or repair threads on screws and bolts. Parting tools cut off parts of the workpiece. They help separate finished pieces from the main material. Each specialized tool serves a unique purpose. They make specific tasks easier and more efficient.
Tool Geometry And Cutting Angles
Turning tools for lathes feature precise tool geometry and cutting angles, crucial for achieving accurate and smooth metal cuts. Properly designed cutting angles enhance efficiency, reduce wear, and ensure high-quality finishes.
Defining Rake, Relief, And Approach Angles
The rake angle helps in controlling the cutting action. It affects chip flow and cutting force. The relief angle prevents the tool from rubbing against the material. Approach angle determines the contact between tool and workpiece. Each angle has a specific role. Proper angles improve tool life and machining efficiency.
The Impact Of Geometry On Machining Performance
Good tool geometry enhances surface finish. It also reduces cutting forces and heat generation. Incorrect geometry can cause tool wear and poor performance. Geometry impacts cutting speed and material removal rate. Optimized geometry ensures better machining performance.
Surface Finish And Tool Selection
Tool material affects the surface finish. Carbide tools offer a smoother finish than high-speed steel. Ceramic tools provide the best surface quality. Each material has different wear resistance. Tool hardness impacts the surface texture. Harder tools create finer finishes. Select the right material for your workpiece.
The right tool ensures a good finish. Tool geometry plays a key role. Positive rake angles help in cutting smoothly. Negative rake angles suit tougher materials. Use a sharp tool for a clean cut. Tool nose radius affects surface smoothness. A larger radius gives a finer finish. Match the tool to the material and finish needed.
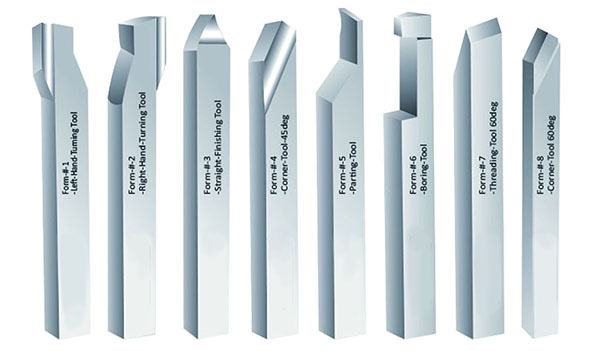
Credit: www.penntoolco.com
Sharpening And Maintenance Of Turning Tools
Always keep your turning tools sharp. Use a grinding wheel for sharpening. Keep the angle consistent while grinding. Use light pressure. Dull tools can cause inaccurate cuts. Use a honing stone to finish. Sharpen your tools regularly for best results.
Clean your tools after every use. Remove any debris or chips. Apply a thin coat of machine oil to prevent rust. Store your tools in a dry place. Regularly check for any wear and tear. Replace worn-out parts immediately. Proper maintenance extends the life of your tools.
Advancements In Turning Tool Technology
New coatings help turning tools last longer. These coatings protect tools from wear and tear. Titanium nitride is a popular coating. It keeps the tool sharp for a long time. Ceramic materials are also used. They are very hard and durable. They can cut faster and stay cool.
CNC machines make turning tools more precise. They help in making the same cuts every time. Automation speeds up the process. It reduces human error. Smart sensors monitor the tools. They alert when a tool needs replacing. This helps in better planning and reduces downtime.
Case Studies: Success Stories In Precision Turning
Precision turning tools have changed many industries. These tools help make better car parts. Factories now make parts faster. The medical field uses these tools too. Doctors need small, perfect parts. Precision tools help make these parts. The aerospace industry also benefits. Planes need strong, light parts. Advanced tools help create these parts.
Precision tools improve product quality. Workers make fewer mistakes with these tools. Factories save money and time. The tools work with many materials. Steel, plastic, and more can be shaped. This flexibility helps many industries. Workers find these tools easy to use. Training takes less time. New workers learn quickly.
Selecting The Right Turning Tool For Your Project
The material of the workpiece is very important. Soft materials need softer tools. Hard materials need harder tools. The shape of the workpiece matters too. Complex shapes need special tools. Simple shapes can use basic tools. Always consider the size of the workpiece. Large workpieces need strong tools. Small workpieces need precise tools.
Budget plays a big role. Expensive tools often last longer. Cheaper tools may wear out fast. Look for value for money. Sometimes, a middle-priced tool is best. Think about tool lifespan. A long-lasting tool saves money over time. Maintenance costs are important too. Easy-to-maintain tools cost less in the long run.
Safety Precautions In Lathe Operations
Ensuring proper safety precautions in lathe operations is crucial. Always use sharp and well-maintained turning tools to prevent accidents. Wearing appropriate protective gear, such as goggles and gloves, enhances safety during the process.
Personal Protective Equipment For Operators
Always wear safety glasses to protect your eyes. Gloves can keep your hands safe. Hearing protection is important for loud environments. Wear a face shield for extra protection. Use a dust mask to avoid breathing in harmful particles. Closed-toe shoes protect your feet from falling objects. Long hair should be tied back. Avoid wearing loose clothing to prevent accidents.
Safe Handling And Storage Of Turning Tools
Always store tools in a dry place. This prevents rust. Keep tools sharp for safe and efficient use. Use tool holders to organize your tools. Label storage areas for easy access. Inspect tools for damage before use. Report damaged tools to your supervisor. Dispose of damaged tools properly to prevent accidents. Clean tools after each use to maintain them. Follow manufacturer’s guidelines for storage.
Frequently Asked Questions
Which Tool Is Used For Turning On A Lathe?
A lathe uses a cutting tool for turning operations. Common tools include carbide inserts, high-speed steel (HSS) tools, and indexable tools.
What Are The 5 Different Lathe Tools?
The five different lathe tools are:1. Turning tool: shapes the material. 2. Facing tool: levels the end of the workpiece. 3. Parting tool: cuts off sections. 4. Boring tool: enlarges holes. 5. Threading tool: creates threads on the material.
What Tooling Do I Need For A Lathe?
You need cutting tools, tool holders, a chuck, a tailstock, a live center, a drill chuck, and measuring instruments.
How Do I Choose A Turning Tool?
Choose a turning tool by considering material, tool geometry, cutting speed, feed rate, and machine compatibility. Select quality brands.
Conclusion
Mastering turning tools for lathe operations can enhance your machining skills. Choose the right tools for precision and efficiency. Keep your equipment well-maintained for optimal performance. By understanding their applications, you can achieve better results. Invest in quality tools to ensure longevity and superior craftsmanship.