Table of Contents
Turning steel on a lathe involves shaping steel by rotating it against a cutting tool. Precision and speed are essential.
Turning steel on a lathe is a fundamental process in metalworking and manufacturing. This technique allows machinists to create precise cylindrical shapes and intricate designs. Lathes use rotating motion and sharp cutting tools to shape and finish steel components. This process is integral in producing machine parts, automotive components, and various industrial tools.
Skilled operators can achieve high levels of accuracy and smooth finishes. Proper tool selection and speed control are crucial for successful steel turning. Understanding the basics of lathe operation and safety protocols ensures efficient and safe machining.
Introduction To Lathe Operations On Steel
Turning steel on a lathe is a precise skill. It shapes steel into many forms. This blog introduces the key operations needed to turn steel effectively.
The Role Of Lathes In Metalworking
Lathes are essential machines in metalworking. They shape and cut metals with precision. Lathes can create cylinders, cones, and complex shapes.
Different lathes serve different purposes. Here are some types:
- Engine Lathes
- Turret Lathes
- Toolroom Lathes
Each type has unique features. Engine lathes are versatile and used widely. Turret lathes handle repetitive tasks well. Toolroom lathes offer high precision.
Unique Characteristics Of Steel
Steel is a strong and durable material. It has unique properties that affect lathe operations. Here are some key characteristics:
Characteristic | Description |
---|---|
Strength | High tensile and compressive strength |
Hardness | Resistance to deformation and wear |
Ductility | Can be stretched without breaking |
Toughness | Ability to absorb energy and resist impact |
These characteristics make steel suitable for various applications. Steel is used in construction, automotive, and machinery. Knowing its properties helps in selecting the right tools and settings for lathe operations.
Setting Up Your Lathe For Steel
Turning steel on a lathe requires precise setup. This ensures safety and accuracy. Below, you’ll find key steps for setting up your lathe.
Choosing The Right Chuck
The chuck is vital for holding your steel workpiece. Three-jaw chucks are common for round workpieces. Four-jaw chucks offer more flexibility but need manual alignment.
Chuck Type | Best For |
---|---|
Three-Jaw Chuck | Round and Symmetrical Pieces |
Four-Jaw Chuck | Irregular Shapes |
Adjusting Lathe Speeds For Steel
Steel requires slower speeds. This reduces tool wear and tear. Check your lathe’s manual for speed settings.
- Low Carbon Steel: 80-100 RPM
- High Carbon Steel: 60-80 RPM
- Alloy Steel: 40-60 RPM
Tooling Selection For Steel Projects
Choose the right tool for the job. High-Speed Steel (HSS) tools are good for most steel types. Carbide tools handle tougher steels.
- Roughing Tool: Removes bulk material quickly.
- Finishing Tool: Provides a smooth surface finish.
- Parting Tool: Cuts off pieces from the workpiece.
Lathe Cutting Techniques For Steel
Turning steel on a lathe requires precision and skill. The techniques used can affect the final product’s quality. This section covers essential techniques for cutting steel on a lathe.
Facing And Turning Basics
Facing is the process of cutting the end of the workpiece. It makes the surface flat and perpendicular to the axis. The tool moves perpendicular to the workpiece’s rotation.
Turning reduces the diameter of the workpiece. The tool moves parallel to the axis. This process can produce cylindrical shapes.
Technique | Tool Movement | Purpose |
---|---|---|
Facing | Perpendicular | Flatten end surface |
Turning | Parallel | Reduce diameter |
Advanced Cuts: Grooving And Parting
Grooving involves cutting a groove into the workpiece. The tool moves perpendicular to the axis. This creates a narrow channel.
- Grooving is used for creating slots or ring grooves.
- The tool width determines the groove’s width.
Parting is used to cut off a section of the workpiece. The tool moves into the workpiece until it separates. This is often the last step in a machining process.
- Parting tools are thin and have a sharp edge.
- They must be aligned properly to prevent tool breakage.
These advanced cuts require careful setup. Proper technique ensures precision and safety.
Precision Drilling On The Lathe
Precision drilling on a lathe is a vital skill for machinists. This process needs care, accuracy, and the right tools. Let’s explore how to achieve precision drilling on a lathe.
Drill Bit Selection For Steel
Choosing the right drill bit is essential. Not all bits are suitable for steel.
- High-Speed Steel (HSS): Good for general-purpose drilling.
- Cobalt Bits: Excellent for drilling hard steel.
- Carbide-Tipped Bits: Best for extremely tough steel.
Always use sharp bits. Dull bits can cause inaccuracies and damage.
Maintaining Accuracy During Drilling
Accuracy is crucial in precision drilling. Here are some tips:
- Use a Center Drill: Start with a center drill to mark the hole.
- Secure the Workpiece: Clamp the workpiece firmly to prevent movement.
- Steady the Drill Bit: Use steady pressure to avoid wandering.
- Coolant Usage: Apply coolant to reduce heat and wear.
Monitor the drilling process. Adjust the speed and feed rate as needed.
Check the depth regularly. Use a depth gauge for precise measurement.
Precision drilling on a lathe requires skill and the right tools. Follow these steps for successful results.
Thread Cutting On A Lathe
Thread cutting on a lathe is a crucial skill in metalworking. This process involves creating threads on a cylindrical workpiece. These threads can be used for screws, bolts, or other fasteners. Precision is key to ensure the threads are accurate and functional.
Tools And Dies For Threading
To cut threads on a lathe, you need the right tools. Threading tools and dies are essential. These are specially designed for cutting threads with precision.
- Threading Tool: This is a single-point cutting tool. It’s used to cut threads on the outside of a workpiece.
- Dies: Dies are used to cut external threads. They come in various sizes and shapes.
- Tap: A tap is used to cut internal threads.
Step-by-step Threading Process
- Setup: Secure the workpiece in the lathe chuck.
- Select the Tool: Choose the correct threading tool or die.
- Align the Tool: Align the tool with the workpiece.
- Set the Lathe: Set the lathe to the correct speed and feed rate.
- Start Cutting: Begin cutting the thread by engaging the tool with the workpiece.
- Check the Thread: Measure the thread with a thread gauge.
- Finish: Complete the threading process and smooth out any rough edges.
Thread cutting on a lathe requires patience and precision. With the right tools and careful steps, you can create accurate and functional threads.
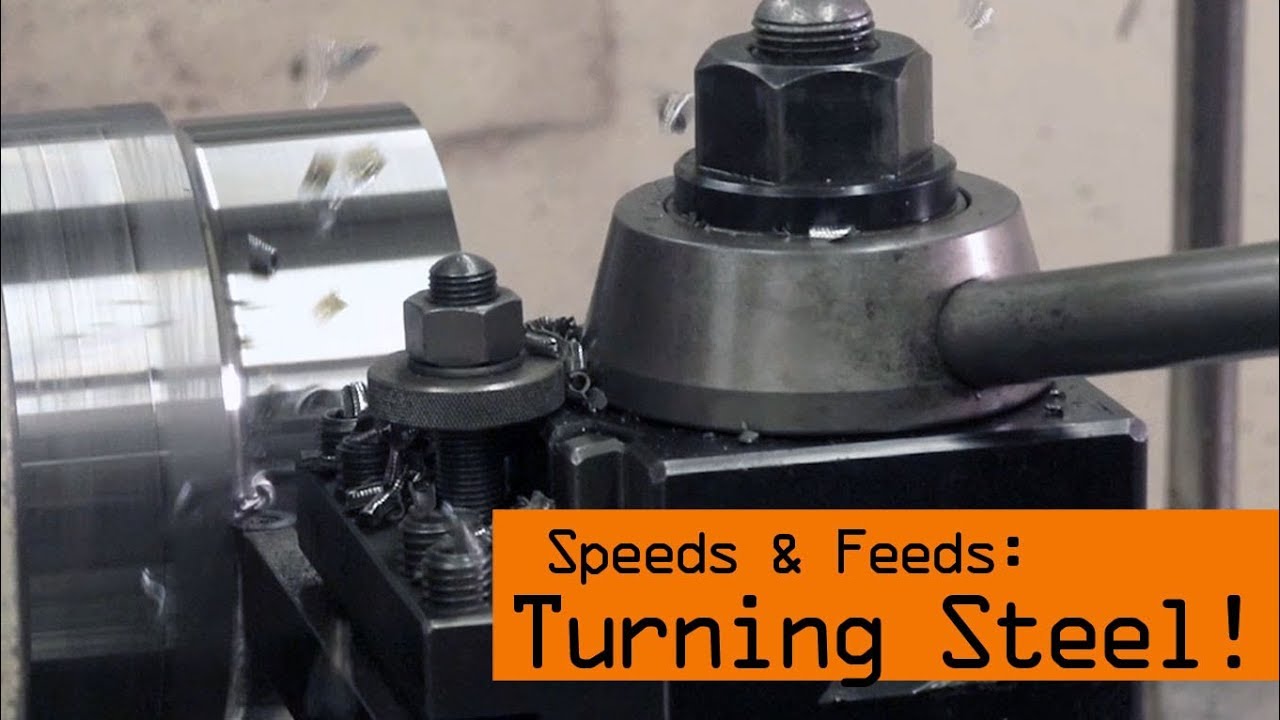
Credit: m.youtube.com
Measuring And Inspection Tips
Turning steel on a lathe demands precision and accuracy. Proper measurement and inspection ensure the final product meets specifications. This section covers essential measuring tools and techniques for tolerance compliance.
Essential Measuring Tools
Accurate measurements are crucial in lathe operations. Here are the key tools:
- Micrometer: Measures small distances with high precision.
- Caliper: Provides quick and accurate measurements of internal and external dimensions.
- Dial Indicator: Measures variations in height or thickness.
- Depth Gauge: Determines the depth of holes or recesses.
- Surface Plate: Provides a flat reference surface for measurements.
Inspection Techniques For Tolerance Compliance
Ensuring your turned steel meets tolerance standards is vital. Follow these inspection techniques:
- Visual Inspection: Check for surface finish, burrs, and defects.
- Dimensional Inspection: Use micrometers and calipers to measure key dimensions.
- Surface Finish Inspection: Compare the surface finish against standards using a surface roughness gauge.
- Runout Measurement: Use a dial indicator to measure any deviation from true rotation.
- Concentricity Check: Ensure the central axis of the turned part aligns properly.
Proper use of these tools and techniques ensures high-quality turned steel parts.
Troubleshooting Common Issues
Turning steel on a lathe can sometimes lead to challenges. Overcoming these issues ensures a smooth and efficient operation. This section covers some common problems and their solutions.
Addressing Chatter And Vibration
Chatter and vibration can ruin your workpiece and tool. To address this:
- Check tool sharpness: Dull tools cause vibrations. Sharpen or replace them.
- Adjust speed: Slow down the spindle speed. This reduces vibrations.
- Secure the workpiece: Ensure the workpiece is tightly clamped.
- Use a steady rest: This provides extra support to the workpiece.
Solving Surface Finish Problems
Poor surface finishes are a common issue. Here are some solutions:
Problem | Solution |
---|---|
Rough Surface | Increase feed rate: A higher feed rate can smooth the surface. |
Tool Marks | Use a sharper tool: Sharp tools leave fewer marks. |
Burrs | Deburr the edges: Use a deburring tool to clean the edges. |
Another tip is to use coolant. Coolant reduces heat and improves the finish.

Credit: waykenrm.com
Safety Practices For Lathe Operations
Turning steel on a lathe requires strict safety practices. Ensuring a safe environment protects both the operator and the equipment. Below, we detail essential safety practices for lathe operations.
Personal Protective Equipment
Wearing Personal Protective Equipment (PPE) is crucial for lathe safety. PPE includes:
- Safety glasses to protect eyes from flying debris.
- Gloves to shield hands from sharp edges and hot chips.
- Hearing protection to prevent hearing damage from loud machinery.
- Face shields for extra facial protection.
- Steel-toed boots to protect feet from heavy objects.
Safe Handling Of Sharp Tools And Hot Chips
Handling sharp tools and hot chips requires caution. Follow these practices:
Action | Safety Practice |
---|---|
Using Tools | Always handle tools by their handles, not the sharp edges. |
Removing Chips | Use a brush or pliers, never your hands, to remove chips. |
Cooling Workpieces | Allow workpieces to cool or use proper cooling systems. |
Always stay alert and focused during lathe operations. Distractions can lead to accidents. Following these safety practices ensures a safer working environment.
Advanced Projects: Taking Skills Further
Turning steel on a lathe is a rewarding skill. Advanced projects can take your skills to the next level. Let’s explore some advanced techniques and projects.
Creating Complex Shapes
Creating complex shapes on a lathe requires precision. Start with a detailed plan. Ensure your tools are sharp and calibrated. Use a steady hand and take your time. Complex shapes may need multiple passes. Always measure twice and cut once. Patience is key to success.
- Choose the right tool for the job.
- Use a caliper to measure accurately.
- Practice on scrap material first.
Complex shapes can include curves, spheres, or intricate designs. Use templates for consistency. A digital readout can help maintain accuracy. Practice makes perfect.
Integrating Cnc Technology
Integrating CNC technology can enhance your lathe projects. CNC stands for Computer Numerical Control. It allows for precise, automated machining. This technology can create intricate designs effortlessly. Here’s how you can integrate CNC into your lathe work:
- Install a CNC controller on your lathe.
- Learn to use CNC software for design.
- Program the CNC to cut your design.
CNC technology can replicate complex patterns. It saves time and reduces errors. Here are some benefits of using CNC:
Benefits | Details |
---|---|
Precision | High accuracy in cuts and designs. |
Efficiency | Faster production with minimal waste. |
Consistency | Replicates exact designs every time. |
Using CNC, you can create complex and precise designs. This technology opens up new possibilities in lathe projects. Enhance your skills and explore new horizons.
Maintaining Your Lathe For Longevity
Keeping your lathe in top condition is crucial for smooth operation. Regular maintenance can extend its life and improve performance. By following some simple steps, you can ensure your lathe remains reliable for years.
Regular Cleaning And Lubrication
Regular cleaning is essential for your lathe. Dust, metal shavings, and grime can affect its performance. Clean the lathe after each use. Use a soft brush to remove debris.
Lubrication is also crucial. Lubricate the moving parts regularly. Check the manufacturer’s guide for the best lubricant. Apply it to the spindle, gears, and other moving parts.
Maintaining a proper lubrication schedule can prevent wear and tear. This simple step can keep your lathe running smoothly.
Detecting And Fixing Wear Issues
Regularly check your lathe for wear and tear. Look for signs of rust, worn gears, or loose parts. Early detection can prevent bigger issues.
- Inspect the spindle and tailstock for alignment.
- Check the bed ways for scratches or dents.
- Ensure the tool post is secure.
If you find any issues, fix them immediately. Tighten loose bolts and replace worn parts. Regular maintenance can save you time and money in the long run.
Keep a maintenance log to track repairs and replacements. This helps in identifying recurring issues and planning future maintenance.
Maintenance Task | Frequency |
---|---|
Cleaning | After each use |
Lubrication | Weekly |
Wear Inspection | Monthly |
Alignment Check | Quarterly |
Follow these steps to keep your lathe in perfect condition. A well-maintained lathe ensures precision and safety.

Credit: www.amazon.com
Frequently Asked Questions
What Rpm Is Needed To Cut Steel On A Lathe?
To cut steel on a lathe, aim for 100-200 RPM. Factors like tool type and steel hardness may adjust this range.
What Speed Do You Turn Mild Steel On A Lathe?
Turn mild steel on a lathe at 60 to 100 surface feet per minute (SFM). Use appropriate cutting tools and coolant.
Can You Turn Metal On A Lathe?
Yes, you can turn metal on a lathe. Lathes are versatile machines used for shaping metals accurately and efficiently.
What Direction Does A Metal Lathe Turn?
A metal lathe typically turns in a counterclockwise direction. This ensures proper cutting and safety during operation.
Conclusion
Mastering the art of turning steel on a lathe enhances both skill and project quality. Practice and precision are key. Remember safety and regular maintenance for optimal performance. With dedication, you can achieve professional results in lathe machining. Happy turning and keep honing your craft for excellence!